一起看看工程机械“隐形冠军”的“野心”
“轰隆隆——”当挖掘机作业的轰鸣声响起时,澳大利亚皮尔巴拉区的一处工地上也再次进入了热火朝天的状态。在这座临近赤道、炎热干旱、室外温度常年37°以上的矿区里,一台超大吨位挖掘机已经连续进行了6000小时的无障碍作业。这样的使用场景,对于身为跨国巨头的主机厂家来说,原本是很正常的作业成绩。然而这一次,他们却不得不暗挑大拇指,因为在这台在海外鏖战的挖掘机身躯里,第一次闪耀着源自中国核心零部件的光芒。
“自主创新能力弱,部分关键核心技术缺失……”在今年5月12日中国工程院举行的《2015年度中国制造强国发展指数报告》新闻发布会上,清华大学副校长、中国工程院院士尤政甩出的这句“狠话”,彻底揭开了中国作为“制造大国”的背后,难以掩饰核心零部件空心化的尴尬。在多年前白益民出版的《三井帝国在行动》一书中,重塑了“中国制造”的概念:中国品牌产品的核心零部件如果不是自己的,只能被称之为“Made in China”(在中国制造)。这引起了国人对于中国制造新的认识。有相关数据显示,长期以来我国发动机、传动系统、液压元器件、控制元器件等关键零部件进口成本占制造成本的40%以上,行业接近70%的利润被外商攫取,尤其对作为国民经济物质技术基础的工程机械行业来说,更是饱受高端核心零部件工业基础薄弱之苦,可谓“如鲠在喉”。
穷则思变,随着“中国制造2025”的提出,中国制造“由大变强”的转型路径第一次如此清晰笃定地呈现在全球目光的聚焦中。尤其面对着压力和紧迫性都很强烈的工程机械制造业升级,核心零部件作为助推自主装备产业崛起的基石,自然也被摆在了“工业强基”的方案桌上。可喜的是,面对核心零部件“封喉”高端制造的窘境,近年来我国工程机械企业界进行了不懈的探索实践,徐工作为中国机械的排头兵,更是早已将研发的触角瞄准核心零部件领域,“中国的工程机械行业解决了90%的难题,但最关键的是要攻克最后的10%。这就如同攀登珠穆朗玛峰最后的几百米,需要聚集更大的力量,用更多的财力、更多的智慧和更多的人才。”正是按照徐工集团董事长、党委书记王民提出的“珠峰登顶论”,徐工液压件公司这家成立于1975年,历经四十余年产业积淀的核心零部件企业,产品不仅遍及全国,更批量出口到欧洲、美国、俄罗斯、日本等近二十多个国家和地区。在各类工程机械、港口机械、环卫机械、煤矿机械、船用设备等行业主机大放异彩的背后,是他们在各细分市场的液压领域中进行着专心致志的耕耘,逐渐成长为肩负引领自主核心零部件产业发展的“隐形冠军”。
深耕研发大国重器的“强基者”
“中国液压也有‘黑科技’!”最近,网上一段世界机器人举重大赛的动画短片火了起来,视频最后成功举起1600吨重物的冠军所用的四缸同步联动锁止技术,就是徐工液压件公司自主研发的一项“黑科技”,至今仍保持着亚洲最大吨位的配套纪录。其实,大吨位起重机油缸一直都是徐工液压件公司的优势产品领域,由于该型产品体积庞大,结构复杂,对可靠性和轻量化的要求极高,作为国内在该领域最早的拓荒者,公司在研发之初面对的也是一片空白,产业发展的历程远比想象的要艰辛的多。
80年代徐工液压件厂貌
八十年代初,随着国家经济建设的繁荣,市场对吊装设备的吨位需求也越来越大。1991年,那时规模仅有几个车间的徐工液压件开始着手大型吊装设备配套油缸的研发工作,而跟随主机开发生产50吨全地面起重机配套油缸的设计工作,落到一位刚进厂不久的大学生肩上,他就是现在“徐州徐工液压件有限公司”的副总经理刘庆教。回忆起第一次独立承担产品设计的经历,刘庆教至今仍颇有感触:“在研发初期,因为没有先例可循,一个现在看起来很简单的设计问题,在当时的情况下真的很难,折腾了近半年的时间,油缸才设计制造出来,然而,能否通过主机验证才是真正的关键。”1991年10月25日,这是一个让刘庆教终生难忘的日子,油缸在主机上的第一天调试,没想到精心设计的导向结构就出了问题,刺耳的噪声中,液压油大量喷出,洒满了他的全身。带着无尽的失落,刘庆教却咬牙继续查阅文献资料,在确定了用金属加非金属‘合金’的方式选型后,进一步优化结构设计,经过四天三夜的攻关,改进型大长薄壁油缸导向防松结构诞生了,谁也不会想到,这项技术衍生结构,足足支撑了大长薄壁油缸25年。后来的试验结果表明,该方法的应用有效解决了长行程油缸的导向难题,不仅为公司日后进行长行程油缸设计研发提供了宝贵的技术经验,也被行业普遍采用,填补了国内相关技术空白。
责任编辑:Jefon
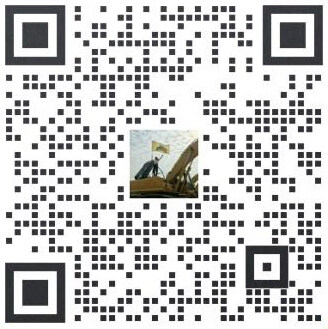
买车卖车 养车维修 疑难故障 学大招
扫码加群 BOSS团同行好友等你交流