发动机再制造的试水之战
编者按:
在中国工程机械行业,“再制造”概念的提出,就像当初“后市场”和“二手机”一样,自提出之日起,就在行业内引起了普遍的关注。然而正如当时业界对于“后市场”和“二手机”赢利存在着诸多质疑一样,再制造在更多人眼里,是一个观念上可以接受,但购买时却鲜有人出手的市场。如何将要报废或者将要进入大修期的设备纳入到再制造的循环中,购买的再制造设备是否能够达到出厂标准,售后服务如何得以保障……这些都是用户在选择再制造设备时的顾虑所在。
在再制造过程中,回收部件的平均再利用率能够达到70%,国外甚至能够达到80%,与新品制造相比,再制造过程中可节省80%以上的水、电等能源消耗,因此,在欧美发达国家,“再制造”已经成为一个规模较大的产业,覆盖国防、汽车、工程机械和电子等多个领域。
据统计,在全球再制造市场的整体份额中,汽车再制造的销售额占据了70%左右。在中国,汽车再制造也是国家重点扶持的项目。2008年3月,国家发改委启动的14家汽车零部件再制造产业试点企业中,潍柴、玉柴和东风康明斯这3家同时从事工程机械配套的发动机企业均位列其中,而发动机行业则无疑成为了再制造领域的先行者。
时隔一年半,这些发动机企业的再制造业务进展如何?对于再制造发动机,中国用户是否能够接受?近期,我们走访了这几家企业,希望通过对发动机再制造这一领域的深入探讨,给致力于工程机械再制造研究的企业一些启示。
发动机再制造能否实现共赢?
据不完全统计,2008年,国内共生产发动机6112万台,其中为工程机械配套的发动机数量接近70万台,按照目前国外再制造发动机每年销量占到新机销量2%~2.5%计算,这个数目将非常可观!
当更多的企业以旁观者的身份来观看这场中国发动机企业再制造的试水之战时,有着30多年再制造经验的卡特彼勒并没有闲着,2009年上半年,卡特彼勒与两家本土代理商合作,分别在顺德、成都建立了面向消费终端的再制造回收点。这是继2005年12月卡特彼勒再制造(上海)有限公司在上海临港工业园区取得营业执照,2006年7月1日正式投入生产运行后,卡特彼勒再制造业务在中国发起的又一记重拳。2009年7月2日,在
沃尔沃建筑设备技术与客户中心落成典礼上,沃尔沃的相关负责人也表示,该中心将会从事零部件再制造业务。与此同时,作为有着50年再制造历史的美国康明斯也已经在湖北投资建设发动机再制造工厂,据相关人士透露,工厂建成之后将负责康明斯再制造发动机的零部件加工和处理工作,东风康明斯则负责再制造发动机的装配。
一场勇敢者的游戏
对于中国发动机企业而言,这场再制造试水之战正在演化成为一场勇敢者的游戏。投资额大、回报周期长、市场规模小、发展前景不明朗,这是发动机再制造行业的一个显著特点。选择进入这个行业,本身就存在着巨大的风险。
追溯中国发动机再制造业务的历史已经有10多年了。最早涉足发动机再制造的中国企业非济南复强莫属,济南复强是目前亚洲唯一一家北美发动机再制造协会(PERA)的会员,也是国家再制造技术研发基地——装备再制造技术国防科技重点实验室的科研教学实践基地。但是即使是这样一家从事发动机再制造已经多年的企业,也面临着很多发展的困惑,赢利水平并不高。
对于像潍柴、玉柴、上柴和东风康明斯这些发动机企业而言,从事发动机再制造也均有一段时间,只是当初没有企业把再制造作为一项赢利的业务来做。起初,企业从事发动机再制造的原因很简单,就是为了将那些三包期内替换回来的发动机的效用发挥到最大,损失降到最低。东风康明斯的胡涛经理说:“三包期内替换下来的发动机,有的几乎和新机差不多,最早我们是为了在内部消化这部分机器,才开始进行发动机再制造的。目前这仍是我们再制造发动机回收的主要来源。”
究竟是什么将发动机再制造由幕后推到了台前?很显然,2008年3月,国家发改委批准的14家整车(机)生产企业和汽车零部件再制造企业中,发动机企业的入选,改变了之前发动机再制造“零打碎敲”的局面,使其开始向“产业化”的方向发展。
对于这些率先试水再制造的发动机企业而言,他们深信“再制造”势在必行,但与此同时他们也并不避讳对于发动机再制造前景的担忧。
为再制造发动机正名
无论是对于制造商、代理商,还是用户,再制造更多的是一种概念,接触过、使用过再制造设备的人可以说是屈指可数。那么再制造与传统意义上的翻新究竟有何区别?它的优势何在?
再制造不是大修或者翻新
近年来,在国内,与工程机械零部件再制造相比,工程机械整机再制造的发展却显得步履维艰。可以说,除了鼎盛天工等个别制造商作为再制造试点企业,试制成功过为数不多的几台再制造产品外,在中国工程机械整机市场上,还没有真正意义上的再制造设备进入流通领域,这些设备更多地停留在大修和翻新的层面。卡特彼勒是再制造领域的翘楚,1973年,卡特彼勒开始涉足再制造,目前再制造业务已经占到卡特彼勒全球营业额的近4%,但从卡特彼勒的再制造清单上,我们看到更多的是发动机、卡车传输装置,甚至军用坦克、火车发动机等,几乎没有整机产品,也就是说,再制造在零部件上最为广泛。
衡量某台产品是否是再制造产品,根本的标志是:再制造产品质量不低于原产品质量标准,(在《汽车零部件再制造试点工作承诺书》上也有所体现),这也是衡量再制造与大修、翻新的主要区别。潍柴再制造公司承诺用户,潍柴再制造发动机的质量与新机出厂标准完全相同,东风康明斯再制造中心也向用户承诺康明斯再制造发动机不低于新机质量标准。
给用户算一笔账
在采访中,潍柴再制造公司总经理李峰给我们算了一笔账。对于进入大修期的发动机,用户可以以相当于新机20%~25%的价格卖给代理商,同时可以以相当于新机70%~75%的价格购得一台再制造发动机,折合下来用户仅用新机一半左右的价格就可购得一台不低于新机质量,与新机享有同样三包服务的再制造发动机。与之相比,大修的费用通常占到新机费用的20%~30%,而且大修之后的设备是无法用新机标准来衡量的。
究竟是付出20%~30%的价格继续使用一台大修后的发动机,还是用50%左右的价格购得一台再制造发动机,用户不妨好好算算这笔账。
将发动机再制造进行到底
在国内,对于再制造产业而言,来自政策层面的支持固然重要,但是更重要的是能够带动整个产业链的发展。现在看来,再制造在中国的推行必然要克服一系列的难点,经历一段较长的时间。
难点一:旧机回收渠道不畅
目前,制约发动机再制造发展的一个重要因素就是旧机回收渠道不畅。迄今为止,国内发动机再制造企业还没有建立起非常完善的旧机回收网络。而在这方面,潍柴是走得比较快的,潍柴已经形成了一套旧机回收鉴定标准,并在2009年6月召集潍柴发动机销量前30位的代理商进行了研讨和商务政策宣讲。李峰说,在做再制造发动机业务时,代理商在旧机回收和再制造新机销售时可以两次获利,两块利润之和将高于销售一台新机的利润。
在鼓励代理商推动再制造发动机的销售方面,企业普遍表示采用了一些鼓励政策,但同时,他们也坦言随着再制造发动机市场投放量的增加,必定会对新机销售带来一定的影响。
难点二:旧机回收标准的制定
在欧美等发达国家,关于再制造发动机的旧机回收已经有一套比较成熟和完善的回收标准,比如美国康明斯再制造公司在这方面已经有多年的积累和经验,东风康明斯与之合作,也将获得这方面的指导,但在国内还处于起步阶段。虽然在二手挖掘机回收方面,南京钢加等企业做过一些探讨,并取得了一些成果,但是就发动机而言,这仍是一个全新的领域。
此外,二手发动机回收与二手挖掘机的回收还面临着一个相似的问题,就是发票及进项税的问题。
难点三:再制造技术仍有待提高
影响再制造业务能否赢利的一个重要因素是回收发动机零部件利用率的高低,利用率越高利润越高,反之利润就越低。目前受再制造技术方面的限制,我国发动机回收件的利用率还不高,还有很大的提升空间。
难点四:用户消费观念的转变
再制造在中国能否发展成为一个产业,很大程度上取决于用户消费观念的转变,而这就要依靠政府以及媒体等对于循环经济和再制造产业的宣传。
发动机再制造能否营造一个制造商、代理商和用户三方共赢的局面?我们相信随着国家对于循环经济的倡导、用户对于再制造产品了解的深入以及再制造工艺技术的提升,这一时刻终会到来。
潍柴 发动机再制造的布道者
正如李峰所言,再制造在实际应用上没有什么太高深的技术,更多的是对制造工艺的精益求精和制造成本的管控。而感动我们的不是潍柴在再制造领域取得的成就,而是企业中有一群像李峰这样为发动机再制造孜孜以求的人。
见到潍柴动力(潍坊)再制造有限公司总经理李峰,是在他二楼的办公室里,潍柴再制造公司管理及行政办公室都是与厂房连在一起的。因为之前对发动机再制造的了解更多地是来自于文字资料,所以在采访之前,李总热情地邀请我们先去车间看一看。每走到一处,李总都会给我们做详细的讲解,关于发动机再制造的种种疑问也迎刃而解。
责任编辑:Anny
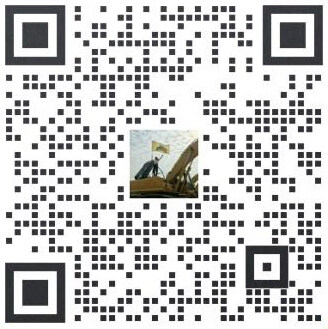
买车卖车 养车维修 疑难故障 学大招
扫码加群 BOSS团同行好友等你交流