内燃机行业国四标准实行 零部件配套是关键
内燃机国四标准将于明年1月1日正式实行,目前国三标准的内燃机已经逐步退出市场。与此同时,与国四发动机相配套零部件的质量问题,将成为国四柴油机是否能保障正常工作的关键。
日前,在中国汽车工业协会车用发动机分会主办的2014年内燃机可靠性技术国际研讨会上,中国汽车工业协会副秘书长叶盛基提出这一现象,他认为:我国内燃机产品可靠性不高是产品在低端市场徘徊的主要原因。
内燃机行业国四标准实行
对于技术要求更加严格的国四柴油机来说,其对配套零部件的要求同样较高,尤其是在其可靠性上提出了更多标准。这给内燃机零部件产品带来了新的挑战,规范各项技术法规,采用通用、成熟的技术路线,提升行业相关标准以促进内燃机可靠性提升,成为业内关注的问题。
升级国四是挑战
对于国四的实行,给内燃机零部件企业带来了新的挑战。东风康明斯发动机有限公司副总经理卢卓华表示:“节能减排要求提高发动机的燃烧效率、气缸压力、热负荷、喷射压力,这些是对内燃机可靠性的挑战,要求内燃机在研发过程中,在新材料应用、零部件耐受、高机械负荷、热负荷、摩擦磨损能力方面有大的提升。”
国四的推行,不仅仅是在内燃机的研发中有更多的技术要求,在生产制造的过程中同样提出了更高的标准,对于加工工艺、加工精度等要求也是越来越高。中国现阶段面临柴油机排放后处理研究起步晚,排放标准升级速度快的特点,而可靠性的研究需要大量的基础数据、实测反馈与改进,短期之内,完成研发、可靠性研究、批产工艺开发、产能快速提升,这无疑是对国内后处理企业的巨大挑战。
据了解,潍柴、玉柴、锡柴和东风商用车等企业在可靠性技术应用领域积极探索,获得了宝贵的实践经验;国内外各科研机构及高校,对内燃机可靠性的基础性研究日益深入并取得了许多阶段性成果,这些都对内燃机行业可靠性技术的研究与应用起到了巨大的推动作用。
发动机核心零部件具有可靠性高、耐久性强、精密度高等特点,发动机主机厂会考虑供应商的历史经验、研发创新能力、生产保证能力、品质保证能力、成本控制能力、财务状况等多方面要素来定点供应商。零部件批量运用于发动机制造前,需要经过手工样件、性能测试、工装样件、台架测试、环境试验、整车道路试验直到小批及大批量生产等多个环节,通常需要耗时两年左右,其开发、验证过程需要大量的人力及资金成本。因此行业显著特点为:供应商定点选择非常谨慎,零部件供应商和发动机厂的合作关系一旦确定后就比较稳定。
目前在国内市场,对于一些技术含量低、附加价值不高,且运输成本较高的发动机零部件基本上已实现了国产化配套;但是对于液压挺柱、液压张紧器、摇臂及可变气门系统等发动机核心零部件,知名汽车主机厂商为了保证产品成功开发、质量可靠,一般采取了谨慎国产化的原则。随着目前国内本土企业的产品质量和技术水平提高,逐步开始从国内本土企业采购。
内燃机再制造成热点
国四柴油机相较以前的发动机成本高,技术更先进,也正因如此在国四柴油机再制造的价值也就更高。前不久,中国内燃机工业协会召开了《内燃机再制造推进计划》推进工作会议。20多个省市的经信委代表参加了此次会议。按照推进计划,到“十二五”末,内燃机工业再制造的生产能力、企业规模、技术装备水平将显著提升,全行业将形成35万台各类内燃机整机再制造生产能力。
内燃机再制造是指将失效的内燃机进行集中拆解、零部件清洗、检测分类,按照原新产品技术规范要求,通过一定的工艺重新加工制造后,使再制造后内燃机产品的使用寿命及其动力性、经济性、环保性、可靠性等指标不低于原型机新机的标准要求。
据了解,与传统废金属回收利用处置方式相比,再制造能够回收报废产品所蕴含附加值的70%左右;与原始制造相比,再制造可节约能源消耗80%、节约材料70%以上,降低制造成本30%~50%;内燃机再制造不仅可以减少废弃物,环境效益可观,而且节能节材,经济效益、社会效益也十分显著。
工信部节能与综合利用司副司长杨铁生表示,历经多年的累积,我国已经步入机电产品报废高峰期,如果固步自封于“大量生产、大量消费、大量废弃”的传统生产和消费模式,不去实现废旧产品循环利用,资源、能源和环境都将难以为继。这就要求我们必须寻求一种可持续的生产和消费模式,加快推进工业循环式发展,以破解能源资源约束和缓解生态环境压力。
中国内燃机工业协会常务副会长兼秘书长邢敏介绍,内燃机工业是我国重要的基础产业,产业链长、关联度高、就业面广、消费拉动大。内燃机使用量大、范围广、热效率高,是目前人类所能掌握的热效率最高的移动动力机械。与汽车产业一样,作为世界内燃机制造大国,内燃机产品的广泛应用和制造产业的持续发展,对保障国家安全和国民经济健康发展至关重要。
去年11月,工业和信息化部发布《内燃机再制造推进计划》,提出到“十二五”末内燃机工业再制造生产能力、企业规模、技术装备水平显著提升的目标。
该计划明确,在内燃机整机及关键零部件再制造示范工程中主要在中重型商用车发动机、乘用车发动机等领域开展再制造示范。在关键配套件再制造示范工程方面,则主要在增压器、发电机、起动机、机油泵、燃油泵、水泵等领域开展示范。
到“十二五”末,全行业形成35万台各类内燃机整机再制造生产能力。建立一批乘用汽车、中重型商用车、工程机械、农业机械、发电设备、船舶动力、石油机械、铁路机车等内燃机再制造示范工程。
零部件配套提升有空间
我国汽车工业由于受重整车轻零部件、重引进轻自主等思想的影响,导致长时间以来,我国汽车零部件行业跟整车行业未能同步发展。目前在国内汽车市场,外资(其中55%为外资独资企业、45%为合资企业)控制了高达70%以上的关键汽车零部件的市场份额,且主要集中在非关键零部件市场。
也正是由于本土零部件企业的发展相对滞后,在国际市场上也很难打开市场,进入海外汽车产业链。而且国内很多汽车厂商,多数是与国外合资生产,零部件等相关产业链本土品牌同样面临进入难的问题。
尤其是在内燃机的零部件领域,目前,国内发动机零部件行业的关键核心技术和核心零部件总成大多为国外大型汽车零部件公司拥有,大多本土自主品牌发动机零部件企业还是以生产技术含量低、附加价值不高的劳动密集型产品为主。核心技术缺乏、研发投入不足、自主创新能力差、管理水平落后、熟练技术工人少等因素都制约了我国本土发动机零部件企业的发展。
虽然我国已成为全球最大的汽车生产市场和消费市场,但随着消费市场向多样化、个性化转变,我国汽车市场已逐渐转变为买方市场,市场竞争将日趋激烈。长期来看,整车价格不断下降将是不可逆转的趋势,单款车型售价总体亦呈下降趋势。
受整车厂降价转嫁成本压力的影响,单一型号的零部件产品必将面临持续的降价压力,因此零部件供应商必须通过不断的提高生产效率、降低成本和扩大产销规模来应对价格下降的压力,同时通过同步研发、超前研发不断地推出新产品及新的型号来扩展新的利润增长点。
所以加大研发投入,学习引进国外先进的设计加工技术,尤其是在国四这类高附加值高技术含量的发动机产品上的技术升级,并逐步实现研发出具有自主知识产权的配套产品,这样中国的发动机零部件行业将获得更大的发展空间。
责任编辑:Eason
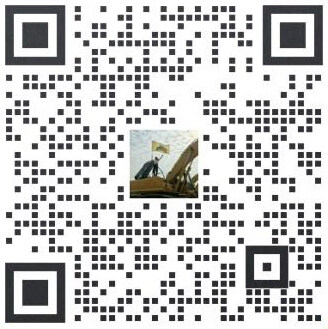
买车卖车 养车维修 疑难故障 学大招
扫码加群 BOSS团同行好友等你交流