我国大型高新起重机研制基地在徐工投产
外国客户为徐工1200吨起重机驻足
五大智能化专有技术成就“世界第一吊”
2002年春天,经过1个多月艰苦卓绝的攻关,在徐工重型诞生了第一根拥有中国人自主知识产权的百吨级起重机圆弧臂,同时攻克的还有全地面底盘悬架等技术,由于抓住了起重机核心技术的“牛鼻子”,徐工一举奠定了十年来在中国起重机核心主流技术上始终超然引领的地位。今天,在研制并产出30吨至1200吨总量7万根高端圆弧形吊臂,制造规模远超世界吊臂制造鼻主-比利时Vlassenroot公司后,徐工新基地再一次突破,大量创新应用了国际领先水平的智能化制造工艺技术,使得我国起重机向世界第一、更大吨位迈进触手可及:
超大型板材数控成型专有技术:超大型起重机圆弧臂成型技术在新基地实现又一个行业新突破:大吨位起重机主臂板材无需对接一次成型。仅此一项技术突破,就创造出年钢材节约15000吨,起重机综合性能反而提升30%的惊人效益。同时还意味着国际市场上,我国大型和超大型高新起重机产品的地位将被重新确立,更高附加值将取代价格优势,展现中国创造新实力。
超大型构件智能化反变形控制技术。工程起重机是我国装备制造业、工程机械产品中工艺制造技术含量最高的品类,尤其是在起重机主体受力结构件变形控制技术上,与大飞机结构件制造技术相当,其共同难点在于超大超长板材在塑型、焊接、变位过程中均会产生难以控制的不规则变形。徐工在行业通用Ansys分析软件的基础上,自主开发出轮式起重机专用结构设计软件,结合对关键件360度破坏性试验,构建起变形量数据库分析系统,自主创新推出了智能化反变形控制技术,切实解决了这一大型结构件成型的国家级难题。在1600吨“世界第一臂”成型现场,世界最高水平的数控成型技术作用下,工程起重机行业最高强度级别的1100型钢材被精准地折弯成圆弧形。不仅如此,在大型吊臂焊接、变位的全过程,这种反变形技术会根据部件受热位置和变位角度的不同,以不同的变形控制和应力释放方式呈现。
智能化激光复合焊接技术和高效双丝焊技术双剑合璧的创新,使刚刚开始摸索完成双丝焊技术的起重机行业,一下子站到了更高层次制造技术平台,两项技术联动,不仅使焊接速度提升1倍,更重要的是确保了每一个焊缝质量一次性达标,真正实现对设计理念的精准还原,为徐工能够攻克“世界第一吊”立下汗马功劳。
智能化焊接变位技术则更具神奇,记者现场看到,焊接机器人根据指令,精准地在部件上滑出一道道令人目炫的焊弧光,而同时,长达15米的“世界第一臂”的构件在变位工装的辅助下,为保证焊缝始终水平而不停地转换着位置,在短短30分钟时间内,“世界第一臂”对焊成型。
在徐工智能化专有技术的支撑下,决定“世界第一吊”核心构件可靠性的关键问题已迎刃而解,等待它们的,是世界级测控技术的考验。
责任编辑:Hermia
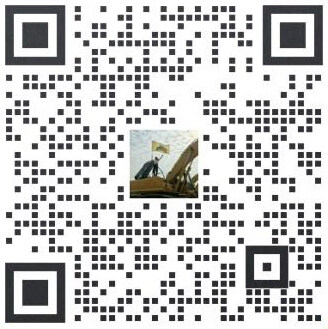
买车卖车 养车维修 疑难故障 学大招
扫码加入BOSS团徐工挖机群