我国大型高新起重机研制基地在徐工投产
近来,徐工频频在国家级高新产品创新、国内外投资、大批量出口、各类研制基地投产等方面加快动作,突显战略亮点,开创出一条中国工程机械企业突出低端竞争重围,引领产业结构升级,全方位提升国际竞争力的新路。
6月25日,伴随着“世界第一臂”的上线和我国第三台QAY1200全地面起重机首次在新基地的下线,预示历时一年半、集合了世界级顶级专家智慧的我国大型高新起重机研制基地成功竣工,顺利投产。这是继徐工2000吨、1000吨履带起重机、1200吨、800吨、500吨全地面起重机扛鼎国家重点工程吊装主力,打破国际大型吊装装备一统天下的神话后,又一项助力我国大型起重机国产装备稳健崛起的创新工程。
我国大型高新起重机研制基地在徐工投产
浩荡车阵,四大起重机械齐登场
集约化制造技术开创四项行业之最
在纵向150米,横向300米的连排车间厂房内走一圈,至少需要30分钟的时间,这就是徐工投资50亿,占地面积1100亩的大型高新起重机研制基地中一个厂房的规模,像这样的厂房共有4座。难怪初次走进基地人总会把世界第一大型起重机研制基地,简单的理解为生产台量的世界第一。
真正占据世界领先地位的,恰恰是隐藏在规模背后的集约化制造技术。
与轿车、重卡大批量、单一品种只需匹配的专用智能化流水线不同,起重机制造工艺技术创新要解决的难题很多,需要精准覆盖近六十种“小批量、多规格”的产品差异化需求,处理好中吨级35种常规产品、百吨级以上25种大型高端产品技术之间的兼容,还要能在集合了全球最多产品品种的生产切换过程中,消除由此极易引发的人、机、物、法、环的浪费,实现高效能、高品质产出。
而基于对未来全球竞争格局的前瞻性预判,徐工也必须围绕“规模占第一、品质世界级、品种全覆盖”这三个看似无法融合的目标定位上闯出新路--在工程机械行业领域首创起重机集约化制造技术,体现了徐工攀顶世界级的高追求。
2009年,徐工与欧美专业研究机构以及国家高端院校合作,重点围绕起重机集约化制造技术可行性展开了工程机械行业“哥德巴赫猜想”,动用了国际领先的模拟仿真设计和分析模型,通过上千次精密计算,最终确定并启动了世界起重机行业独有的经纬线协同并行式工艺组合技术。简单的说,经线工艺技术提供了批量高效生产的线性化解决方案,纬线工艺技术解决了多品种柔性切换的难题,在徐工物联网和信息化技术的强大支撑下,构建了徐工集约化制造技术的庞大核心体系:
在全球最大的起重机焊接生产线上,一个占地仅50平米的三维柔性工装系统就能满足20余种小到5米大到15米桁架臂的拼装焊接,在30分钟内就能完成3种型号桁架臂的柔性切换指令,这在大型化多品种产品制造中是极为罕见的。
在行业唯一的百吨级以上起重机装配生产线上,每隔80分钟就会自动向前递进一个工位,而零部件实时配送系统、智能化在线监测系统,能够满足单品种批次产出的同时,容纳6种不同型号的百吨级以上起重机在线装配。世界首台最大吨位全地面起重机底盘就是刚刚从这里下线。
行业独有“线性化整机涂装系统”,打破千吨级产品大型零部件露天喷涂、手工作业传统,达到世界领先水平……这些仅仅是徐工集约化制造技术中的一个缩影,据了解,在新基地20余条现代化生产线上,徐工专有柔性工装创新专利技术就有12项。
徐工起重机集约化制造技术创造了巨大的经济价值,也同时开创了四项行业之最:起重机现代化柔性生产线由行业最大到70吨提升至千吨级以上;覆盖产品品种由行业平均15种提升到60种;单位产值达1000万/亩/年,超出国际同类企业最高水平50%;大吨位起重机由月产40台直线一跃提升至月产超100台,直逼国际巨头霸主地位。
外国客户为徐工1200吨起重机驻足
五大智能化专有技术成就“世界第一吊”
2002年春天,经过1个多月艰苦卓绝的攻关,在徐工重型诞生了第一根拥有中国人自主知识产权的百吨级起重机圆弧臂,同时攻克的还有全地面底盘悬架等技术,由于抓住了起重机核心技术的“牛鼻子”,徐工一举奠定了十年来在中国起重机核心主流技术上始终超然引领的地位。今天,在研制并产出30吨至1200吨总量7万根高端圆弧形吊臂,制造规模远超世界吊臂制造鼻主-比利时Vlassenroot公司后,徐工新基地再一次突破,大量创新应用了国际领先水平的智能化制造工艺技术,使得我国起重机向世界第一、更大吨位迈进触手可及:
超大型板材数控成型专有技术:超大型起重机圆弧臂成型技术在新基地实现又一个行业新突破:大吨位起重机主臂板材无需对接一次成型。仅此一项技术突破,就创造出年钢材节约15000吨,起重机综合性能反而提升30%的惊人效益。同时还意味着国际市场上,我国大型和超大型高新起重机产品的地位将被重新确立,更高附加值将取代价格优势,展现中国创造新实力。
超大型构件智能化反变形控制技术。工程起重机是我国装备制造业、工程机械产品中工艺制造技术含量最高的品类,尤其是在起重机主体受力结构件变形控制技术上,与大飞机结构件制造技术相当,其共同难点在于超大超长板材在塑型、焊接、变位过程中均会产生难以控制的不规则变形。徐工在行业通用Ansys分析软件的基础上,自主开发出轮式起重机专用结构设计软件,结合对关键件360度破坏性试验,构建起变形量数据库分析系统,自主创新推出了智能化反变形控制技术,切实解决了这一大型结构件成型的国家级难题。在1600吨“世界第一臂”成型现场,世界最高水平的数控成型技术作用下,工程起重机行业最高强度级别的1100型钢材被精准地折弯成圆弧形。不仅如此,在大型吊臂焊接、变位的全过程,这种反变形技术会根据部件受热位置和变位角度的不同,以不同的变形控制和应力释放方式呈现。
智能化激光复合焊接技术和高效双丝焊技术双剑合璧的创新,使刚刚开始摸索完成双丝焊技术的起重机行业,一下子站到了更高层次制造技术平台,两项技术联动,不仅使焊接速度提升1倍,更重要的是确保了每一个焊缝质量一次性达标,真正实现对设计理念的精准还原,为徐工能够攻克“世界第一吊”立下汗马功劳。
智能化焊接变位技术则更具神奇,记者现场看到,焊接机器人根据指令,精准地在部件上滑出一道道令人目炫的焊弧光,而同时,长达15米的“世界第一臂”的构件在变位工装的辅助下,为保证焊缝始终水平而不停地转换着位置,在短短30分钟时间内,“世界第一臂”对焊成型。
在徐工智能化专有技术的支撑下,决定“世界第一吊”核心构件可靠性的关键问题已迎刃而解,等待它们的,是世界级测控技术的考验。
高端测控技术引领数字化革命
真正的数字化革命,不仅是配置一套可在线查询图纸的可视化终端那么简单。
测控技术无处不在。从大型激光切割机启动切割的那一刻起,作为“世界第一吊”结构件的一部分,编号为XZQ10002201的板材,就在庞大的数字管理系统中留下了自己的印迹。同样,组成起重机庞大身躯的上万种大大小小的部件,包括液压、电器都在数字管控中枢中留下永久的身份编码。微小异动会在第一时间传递到指定工位,以便于工人及时纠偏。这种数字化管控覆盖到方方面面,即便是最智能的机器人也不例外,每一个焊接过程的数据都要被实时“捕获”和分析,每一个焊缝质量都得到及时探测,哪怕是焊弧滑过时一个微小的抖动都会在监控系统中一览无余。
实时体检全程掌控。想知道“世界第一吊”的“血压”是否正常吗?2秒钟就可以知道答案,这不是科幻,徐工自主开发的装配在线检测系统让这一切变得简单。在装配线上有一组不起眼的装置,由上百个肉眼难以察觉的感应“电子眼”组成,机器行进到关键工位装配完工时,都会被自动“体检”一遍,时间只需5分钟。全部装配完成后,整车还将接受检测系统对其“回转、伸缩、卷扬”等等多个主系统和子系统运行的大考。10分钟后一张全方位的体检表呈现在系统终端,问题点会通过报警的方式同步显示出来。
很难想象,假如“世界第一吊”的超级巨臂装到整机上进行吊重试验时,才发现吊臂受力抖动的问题,将带来多大的麻烦。大量的整机拆解返工浪费不说,吊臂内部问题的识别也变得异常艰难。如今,徐工集合十年的吊臂检测经验,自主研制开发的智能化吊臂试验台,可以模拟各种实际作业工况,在线完成吊臂内部机电液、以及所有功能和性能的测试。
全生命周期管理。测控技术不仅仅覆盖了焊接中心、整机装配线、吊臂试验台、底盘检测线,在徐工大型高新起重机研制基地20条现代化生产线上,乃至正销往世界各地的设备上,都实现了物联网技术和ERP、MES、SRM、CRM、BI等现代化管理系统全面融合,实现了产品全生命周期管理。徐工重型的高管,只需通过系统,就能实时查阅到各类数据报表,和自动呈现出的各类异动分析。
徐工正通过数字化技术,发起一场覆盖起重机产品全生命周期测控技术的革命,在信息化和工业化“两化融合”的道路上大踏步前进。
我国大型高新起重机研制基地在徐工竣工投产,带给人们对徐工“国际化、千亿元、世界顶级企业”地无限遐想,中国自主研制的大型工程起重机势必在世界范围形成巨大影响。
责任编辑:Hermia
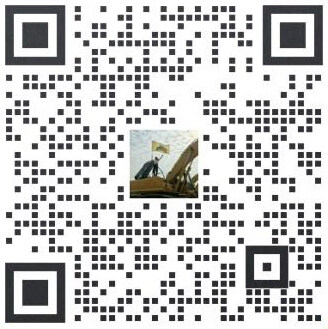
买车卖车 养车维修 疑难故障 学大招
扫码加入BOSS团徐工挖机群