基础薄弱造成技术空心 “山寨”路几时走到尽头
关于“九千亿”的话题之三:
在不久前的日本地震救灾过程中,三一重工62米臂长、被日本媒体称之为“大麒麟”的泵车曾与德国56米臂长、有着“大象”称谓的泵车在福岛核电站周边“八仙过海,各显神通”。此后,30辆长臂泵车意向订单由日方交予三一重工。虽然没有人会因此就热衷于“大麒麟”与“大象”之间有关成败之类的话题,但“大麒麟”能在这样的时点向全世界展示自己,已经足够令人兴奋了。
随着产业结构的迅速升级,技术研发能力的不断提高,中国工程机械行业在产品的高端、大型、智能化方面取得了长足进步,不仅彻底打破了大型和超大型工程机械产品长期依赖进口的局面,而且以三一重工、中联重科、徐工集团为代表的工程机械行业龙头企业,在国际工程机械产业领域正展现出强劲的上升势头和日益增强的影响力。而具有世界级水平的500吨、1200吨级全地面起重机、2000吨级履带式起重机、世界最长臂架的混凝土泵车、全球最大的水平臂上回转自升D5200-240塔式起重机等产品的纷纷涌现,使中国工程机械行业已经成为中国装备制造业中水平最高、核心能力最强的代表。
不过,正如中国工程机械工业协会理事长祁俊所坦言,虽然中国工程机械企业这些年取得了很大的进步,但无论是在技术水平、技术创新能力以及产品层次上,与国外先进企业还有不小的差距。中国工程机械行业必须围绕以结构调整和发展方式转变为主线,大力推进“调整转型,创新升级”战略,通过发展高端、大型、智能化工程机械和关键配套体系领域,推动行业健康、持续的快速发展。
应该清醒地看到,中国工程机械技术升级的途径主要以外部引进消化吸收为主,原始创新很少,集成创新更有待大力加强。而与主机产品迅速发展形成巨大反差的是,基础零部件和基础工艺发展严重滞后。与主机配套的发动机、变速器、驱动桥、高压大流量的泵、阀、密封件、高强度紧固件等基础零部件质量可靠性差,品种规格不全,特种原材料等长期依赖进口。中国工程机械要在更高的层次上体现出竞争力,这道“坎”是必须迈过去的。
基础薄弱造成技术“空心”化
关键零部件和基础工艺发展严重滞后的局面,已成为目前制约中国工程机械行业进一步提升竞争力的“瓶颈”因素,在一定程度上,甚至成为了一个难以破解的“死结”。
以挖掘机为例。目前国内挖掘机生产的模式大致为:以国内外可采购资源为支撑的产品集成。也就是说产品由“美国的发动机,德国的液压系统,日本的电控系统,再加上国内的车架结构件”等组装而成。或者是“引进—测绘—制图—装配—改进—成型”的克隆模式。而在产品的核心工作部以及关键零部件上,国内产品的水平差距较大。这使得国内品牌挖掘机的“山寨”现象普遍存在。由于关键零部件受制于人,使生产过程中的被“掣肘”自然成为一种无奈。而仅作为只是不掌握核心技术的产品制造商和组装商,其发展抑或是可持续性显然缺乏保障。
有业内人士指出,现在的情况已不单单是探索如何提高关键配套件水平的问题,而是要积极探索在多长时间内能够赶上世界先进水平的问题。
据悉,三一重工、中联重科以及柳工等企业都投入大量精力研发高压液压装置。有评论认为,从目前各企业的研发能力和进展情况来看,要实现高水平液压装置的本土产业化还需要三至五年甚至更长时间。但与此同时,一些外资企业正加快在中国投资建厂的脚步。而一旦这类尚属“垄断性产品”的优势地位继续得到加强的话,对国内企业而言,后果是不难想像的。
在专家看来,工程机械制造业的自主创新方面还存在很多不足:
首先是在技术来源上存在问题。在工程机械制造业的技术供应链中,企业的技术一般有三个来源:由社会的公共技术研究平台提供;企业通过引进技术及消化吸收后所形成的技术;企业自主的原创性技术。随着科技体制的改革,原属于产业部门公共性质的研究机构转制成企业,经营性身份的确定使其没有义务和能力再从事共性技术研究。这使得原来为广大企业提供共性技术,为行业提供技术来源的这部分功能基本消失。同时,从国家整个创新体系上,产业的创新体系构成缺位,导致在结构上共性技术研究的缺位。而要解决这一难题,还有赖于公共资源的介入与支持。
其次是作为自主创新主体,同时也是最活跃的企业在创新过程中所发挥的作用明显不足。目前,国内企业研发经费投入的强度偏低。虽然较以往有明显增加,但与那些国外竞争对手相比,差距甚远。比如,缺乏高性能实验台及试验方法被认为是制约行业发展的一个重要因素。有业内人士指出,目前国内企业普遍缺乏高精尖技术,关键就在于实验和检测平台的投入明显不够。实验做得少,导致数据积累不够,没有数据库支撑,创新就无从谈起。也许是意识到此,近来一些千万级别的实验台已在投建中。
只引进不消化终是要还账的
事实上,所有技术后进国家都是从引进、采用和吸收进而实现超越的。但其中的成功者都能够保证,当它们被原有的市场领先者视为威胁时,其企业已经形成了一定的自主创新能力,并有能力继续向国际技术前沿迈进。
上世纪70年代末,中国曾引进德国力士乐公司液压装置的技术和生产工艺。有业内人士介绍,当时引进技术曾在行业内扩散,目前在液压行业内仍保有四套完整的技术资料。只是这些技术并未被完全消化吸纳。而其中的原因应该说是既简单又复杂。说简单,就是长期以来在装备制造业的体系构建过程中,重主机轻部件的发展模式所导致的后果。说复杂,就是将国外百年走过的发展历程,浓缩至几十年甚至十年内完成的主观诉求,必然会造成产业在内涵方面的单薄。而通常的观点是:国内配套件企业大多属于中小型企业,行业内年销售规模能达到10亿元的企业屈指可数。因此,在消化吸收和资金投入等能力方面明显不足。
有业内人士指出,这些年来,工程机械行业用在引进技术和消化吸收上的投入并不少,但通常是引进技术花1元,用于消化吸收才0.2元。而日韩则是引进技术花1元,在消化吸收上投入七八元。因此,看上去花钱不少,但技术的从属地位根本体现不出应有的附加值。
记者两年前在做调研时,一家液压企业负责人的说法至今仍给人留下深刻印象。在他看来,再从国外引进液压技术的理由其实并不足够充分。因为,就是连30年前引进的技术我们至今都没能真正掌握,而技术的发展是有内在联系和延续性的,如果技术路线不变,那么,提升的部分是相对有限和容易了解把握的。只要我们能下大力气掌握已有的引进技术并完成产业化,就将使国内的液压装置水平实现一个质的飞跃。在此基础上才谈得上创新提高。
尽管实验能力有限,但当时该企业的相关技术实验包括大量共性技术实验都在24小时运转。他们还投入大量资金与冶金企业合作,试图解决基础原材料的适应性问题。而这种情况在液压行业中并非个例。当然,少数企业的努力并不能掩盖整个产业体系在消化吸收方面投入薄弱的状况。
另一个妨碍零部件发展的因素是,主机企业与零部件企业之间难以形成一个利益共同体,以相互合作,相互支持,相互包容的态度破解难题。在这方面尤以液压部件为典型。在主机企业看来,液压件生产企业普遍规模偏小,单个企业从配套能力上很难满足主机企业的需求,加之产品在可靠性上的不足,致使选配的积极性不高。而配套企业则认为,主机企业的强势地位已经降低了配套供应商的侃价能力,既然你的进入门槛高,且缺乏选配的积极性,那我就没必要在你那个产品上多做投入。你干你的,我干我的,井水不犯河水。长此以往,不能说双方老死不相往来,但造成供应链阻滞的现象的确存在。
目前有观点认为,配套件企业与整机企业实现整合,集合双方的资源,以整机带动配套件的发展,进而促进整个行业技术的提升,不失为一个可行之道。但在记者看来,目前主机企业整合国内关键零部件企业特别是核心企业的难度,不亚于其正在积极实施的海外并购。其中的缘由非常微妙。此外,业内谈论较多的配套件企业之间联合研发的模式,估计在短期内也难以产生实质性成果。
目前,中国企业正日益被视为有力的竞争对手,并面临着严格的技术进口条件和不断减少的可供引进的技术,甚至以市场换技术的初衷都难以实现。而随着国际产业转移的不断深化以及受中国市场巨大容量的吸引,产能的转移仍在持续地进行中,但核心技术的获得仍面临较大的障碍。对此,中国企业的自主创新能力看来还不足以迎接这样的挑战。当传统方式不能达到目的时,那么,对新路径的探索与尝试就是必须的了。
(未完待续)
责任编辑:Daisy
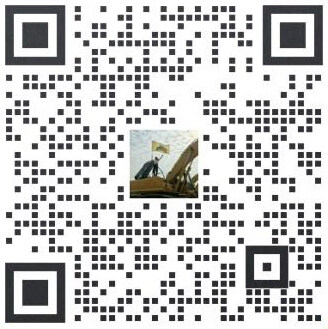
买车卖车 养车维修 疑难故障 学大招
扫码加群 BOSS团同行好友等你交流