中国核电自主化再提速 装备制造完成“十年生聚”
“政产学研用”构建协同创新体系
近年来,依托中国25台在建核电机组逾2000亿元总投资的巨大市场,带动了整个产业链5400多家企业共同发展。
其中,以一重、二重、上重为主的大型重装企业通过在主设备大型铸锻件方面的攻关,从红沿河一期工程开始,主设备大型锻件开始实现国产化突破,红沿河1号机组也成为首次采用国产主设备大型锻件的国内商用核电机组。目前已全面掌握百万千瓦级核电机组核岛主设备大型铸锻件的关键技术和工艺,实现完全自主化。
以东方电气、上海电气、一重、哈电重装、ADJV等企业为主的核岛主设备制造企业,在岭澳二期工程实现国产化的经验基础上,设备加工、成型、装配能力全面提升。除部分关键部件外,已经实现红沿河、宁德、阳江(包括福清、方家山、昌江等)项目的反应堆压力容器、蒸汽发生器、稳压器、堆内构件、安注箱、硼注箱、控制棒驱动机构、主泵、主管道和环吊等核岛主设备的独立供货任务。
以沈鼓、深蓝、重庆水泵、阿波罗等企业为代表的核电水泵的自主化取得了骄人的成绩。7种核二级泵均已完成鉴定,部分已完成制造并予以供货。
以大连大高、中核苏阀、苏州纽威、江苏神通等企业为代表的核级阀门制造企业完成了现阶段国内在建项目超过百分之九十的闸阀、截止阀和止回阀的供应,率先突破核一级截止阀在国内商用核电站的国产化,实现部分核级安全阀国产化,部分气动调节阀国产化;全部蝶阀、球阀实现国产化;95%隔膜阀实现国产化。
以保变、沈变、西变、陕柴等企业为主的电气设备供应团队已全面实现主变压器、厂用变压器、辅助变压器、应急柴油发电机组的自主化供应。
另外,在主管道、主蒸汽管道、核级碳钢大口径管道预制、支吊架、20控Cr钢管、Wb36CN1高压管道、部分核级碳钢和不锈钢板材等方面,目前已经相继实现了国产化突破,并已在红沿河与宁德等核电项目上实现了国产化供货。中广核在建CPR1000堆型核电站全部十四台非安全级仪控系统供货实现全部国产化,安全级仪控系统实现集成总包。
综合来自这些企业的信息可以认为,近年来,中国核电装备制造企业不仅在“卡脖子”的大家伙上实现了从无到有的长足进步,在“电、密、仪”这些精密设备和核电站“神经系统”的部件上也攻克了一座座堡垒,发电机、电气贯穿件、核级密封、仪控系统等相继研发成功,不仅证明了中国制造业有能力啃下“硬骨头”,也再一次验证了实施装备国产化的重要战略意义。
业内人士认为,这种局面的形成,与中国核电装备制造产业形成了核电企业和装备制造企业通过构筑以“政产学研用”一体为特征的协同创新体系有直接关联。
所谓“政产学研用”协同创新,实质是技术产业化的过程,其目的是希望贯通政策引导(政)、需求牵引(产+用)、技术推动(学+研)各环节,发挥上述环节的协同效应,实现技术升级和技术掌控、拓展服务范围,形成新的业务增长和资产增值。
“走出去”获得坚实基础
随着国家高层领导不断力推,中国核电技术及产品已经逐步打开国际大门。但如果没有自主化核电装备的“走出去”,中国核能工业“走出去”成效必将大打折扣。
目前,实现高国产化率、见证中国核电产业自主化进程的岭澳二期,红沿河1、2号机组,宁德1、2号机组,阳江1号机组自投运以来,运行状态良好,能力因子均达到或高于世界核电运营者协会(WANO)国际标杆的中间水平。
事实上,这些成绩的取得,与国产化设备的质量和可靠性密不可分。而这也使得中国核电装备制造和核电建设完全有信心、有能力回应“走出去”的国家召唤。
国家能源局科技装备司司长黄鹂在一次接受采访时说,自己目睹了核电国产化联合研发中心已经走过的5年历程,“衷心地希望下一个5年乃至10年、20年……”
可以相信,在外部政策的强力支撑和领军企业的积极推动下,中国核电装备产业未来完全有能力解决“强而不大”、协调好产业竞争秩序、优化产能布局等挑战,届时,随着中国核电装备制造业的国产化能力更上一层楼,“中国制造”核电站在全球布点的光明前景终将得到实现。
责任编辑:Nora
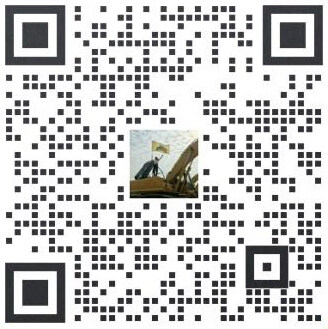
买车卖车 养车维修 疑难故障 学大招
扫码加群 BOSS团同行好友等你交流