浙大盾构自主设计制造关键技术团队创新纪实
向着“中国设计中国造” 掘进
20多年前,一种叫“盾构”的大型掘进机械装备开始进入中国,改变了手镐、钢钎、炸药、小火车运土等传统的隧道施工方法。
无论是在山间、水底,还是在城市地下,“盾构”就像一辆在黑暗中开路的“火车”,削吞土石,缓缓吐送到身后的传送带上。同时,一块块拱型预制件被转举到需要的位置,拼接成坚固的隧道拱圈,隧道掘进、排土、衬砌一次成型。
然而,一台进口的普通盾构机价格是上亿元人民币,且维修费用惊人。好在如今,这种“洋盾构”一统天下、隧道施工受制于人的局面终于得到改变。浙江大学与国内多家龙头企业进行了长期稳定的产学研合作,经过持续12年的盾构关键技术攻关,不仅实现了盾构的“中国设计、中国制造”,还实现了与“德国制造”、“日本制造”、“美国制造”的平等国际竞争。
近日,这项由浙江大学领衔的高校和企业联合的“盾构装备自主设计制造关键技术及产业化”科研团队,摘取了2012年度国家科学技术进步奖一等奖。
组建盾构“国家队”
上世纪90年代,中国的城市地铁建设率先在北京、上海、广州等地铺开,地铁隧道掘进的工地里,被“洋盾构”赚取着高额的利润。
浙大机电所的学者们认识盾构,是从诊治“水土不服”的洋盾构开始的。1995年,国家“九五”重点工程――西安安康铁路咽喉工程秦岭隧道上马。施工方中铁隧道从德国进口了一台掘进机。然而当秦岭隧道将要完工的时候,机器坏了!德国厂家说要换液压装置,新装置两年后才能到。中铁只好把求救电话打到浙大机电所。
从此,随着中国进口的“洋盾构”越来越多,浙江大学机电控制工程研究所的杨华勇和魏建华两位教授就成了盾构的临时“急诊医生”。他们在“治病”的过程中发现,盾构中很多问题需要研究,于是开始申请国家自然科学基金的面上和杰出青年基金项目。2002年,国家“863”计划机器人主题启动了对盾构项目的支持。
杨华勇主持召开了多次跨地域的全国性技术论证会,收集、汇总、分析来自国内外隧道施工现场和设计制造生产第一线的难题,最终凝练出盾构技术的攻关目标:首先是安全问题,国内外隧道掘进工程时常发生地面塌陷事故;其次是掘进工效问题,盾构施工经常发生装备关键部件失效,影响掘进效率;三是导向精度问题,盾构掘进方向跑偏,影响隧道质量。这三大问题是长期困扰行业的国际难题。
浙大参与盾构的科研团队也逐渐从杨华勇和魏建华两人增加到4位教授、两位副教授和多位研究生,杨华勇牵头负责,魏建华负责驱动系统,陈大军负责电控系统,龚国芳负责实验平台……
企业的事,国家的事
合作中,浙大的科研团队主要从事电液驱动、推进和控制系统的研发,这是国外技术封锁最严重的部分,也是盾构隧道工程施工中出现失稳、失准和失效三大国际难题的根本所在。
2004年,浙大研制出了具有自主知识产权的电液驱动和控制系统样机。对于这项新技术,很多施工企业都不愿意“冒险”尝试。直到有一次,上海地铁施工因为突然停电,一台洋盾构“趴窝”了。杨华勇和魏建华带着自己的宝贝到了现场,先修好了洋的,却换上了土的。一启动,大刀盘开始正常发力。待使用一切正常,施工方才知道接上去的是“中国造”。
“浙大学者们针对盾构地下作业‘失准’的国际难题,提出的解决方案很有用。”上海隧道工程股份有限公司盾构制造分公司总经理张闵庆说,“我们企业负责产的部分,大学负责学研部分,即基础理论的研究、尤其是设计方法的研究。这些方法和新思路设计对我们具体的系统与部件的集成和元器件的研制,起到了很好的作用,支撑了产的部分完成,最终使产品的全部系统和整机性能完全达到隧道施工的要求。”
目前,持续十多年校企合作中的研究成果已用在了全国超过四家盾构整机龙头生产企业,实现了盾构装备自主设计和产业化批量生产与应用,陆续建成了多个盾构产业化生产基地。与全球主要盾构制造商的产品相比,主要技术指标达到同等水平,个别性能指标甚至优于国外盾构。
永不终止的联合
“我们是为企业服务,为行业服务的。”这是杨华勇常挂在嘴边的一句话。由于盾构需要根据不同的地质条件,对不同系统进行量体裁衣式的设计,因此需要多学科专业人员的交叉努力,杨华勇从自己带领的机电团队和机械系开始,通过“973”项目的运行机制与浙大控制系和土木建筑学院的教授们合作,希望对盾构整个产业链都提供力所能及的技术服务,学研的合作伙伴扩大到了国内另外7所院校,包括机械、土木、力学和控制四个一级学科的不同学者。中国铁建重工集团等大型企业也加入,成为紧密型的研发合作伙伴,产学研的协同创新研究道路将越走越宽广。
当前,中国早已成为隧道建设大国。杨华勇说:“未来十年,我国还将新建隧道超过1万公里,需要新增盾构超过1000台,拉动相关直接投资1万亿以上。我国是盾构需求最大的国家,已占全球市场的60%。大学和企业的产学研合作还将继续‘掘进’。”
责任编辑:Alley
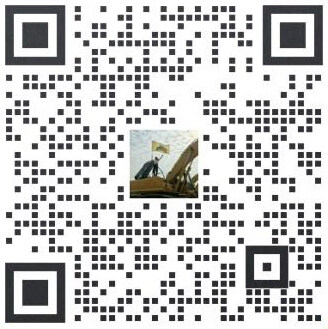
买车卖车 养车维修 疑难故障 学大招
扫码加群 BOSS团同行好友等你交流