“世界第一臂”徐工开启全地面起重机巨章
看今朝,独领风骚
今天,在研制并产出30吨至1200吨总量7万根高端圆弧形吊臂,制造规模远超世界吊臂制造鼻主-比利时Vlassenroot公司后,徐工新基地再一次突破,大量创新应用了国际领先水平的智能化制造工艺技术,使得我国起重机向世界第一、更大吨位迈进触手可及:
1、超大型板材数控成型专有技术:超大型起重机圆弧臂成型技术在新基地实现又一个行业新突破:大吨位起重机主臂板材无需对接一次成型。仅此一项技术突破,就创造出年钢材节约15000吨,起重机综合性能反而提升30%的惊人效益。同时还意味着国际市场上,我国大型和超大型高新起重机产品的地位将被重新确立,更高附加值将取代价格优势,展现中国创造新实力。
2、超大型构件智能化反变形控制技术:工程起重机是我国装备制造业、工程机械产品中工艺制造技术含量最高的品类,尤其是在起重机主体受力结构件变形控制技术上,与飞机结构件制造技术相当,其共同难点在于超大超长板材在塑型、焊接、变位过程中均会产生难以控制的不规则变形。徐工在行业通用Ansys分析软件的基础上,自主开发出轮式起重机专用结构设计软件,结合对关键件360度破坏性试验,构建起变形量数据库分析系统,自主创新推出了智能化反变形控制技术,切实解决了这一大型结构件成型的国家级难题。在1600吨“世界第一臂”成型现场,世界最高水平的数控成型技术作用下,工程起重机行业最高强度级别的1100型钢材被精准地折弯成圆弧形。不仅如此,在大型吊臂焊接、变位的全过程,这种反变形技术会根据部件受热位置和变位角度的不同,以不同的变形控制和应力释放方式呈现。
3、智能化激光复合焊接技术和高效双丝焊技术:双剑合璧的创新,使刚刚开始摸索完成双丝焊技术的起重机行业,一下子站到了更高层次制造技术平台。两项技术联动,不仅使焊接速度提升1倍,更重要的是确保了每一个焊缝质量一次性达标,真正实现对设计理念的精准还原,为徐工能够攻克“世界第一吊”立下汗马功劳。
4、智能化焊接变位技术则更具神奇:记者现场看到,焊接机器人根据指令,精准地在部件上滑出一道道令人目炫的焊弧光,而同时,长达15米的“世界第一臂”的构件在变位工装的辅助下,为保证焊缝始终水平而不停地转换着位置,在短短30分钟时间内,“世界第一臂”对焊成型。
5、高端测控技术引领数字化革命:真正的数字化革命,不仅是配置一套可在线查询图纸的可视化终端那么简单。从大型激光切割机启动切割的那一刻起,作为“世界第一吊”结构件的一部分,编号为XZQ10002201的板材,就在庞大的数字管理系统中留下了自己的印迹。同样,组成起重机庞大身躯的上万种大大小小的部件,包括液压、电器都在数字管控中枢中留下永久的身份编码。微小异动会在第一时间传递到指定工位,以便于工人及时纠偏。
徐工装配检测线上一组不起眼的装置让实时体检、全程掌控变得简单,这是由上百个肉眼难以察觉的感应“电子眼”组成的监控装置,机器每行进到一个关键工位装配完工时,都会被自动“体检”一遍,时间只需5分钟。全部装配完成后,整车还将接受检测系统对其“回转、伸缩、卷扬”等等多个主系统和子系统运行的大考。10分钟后一张全方位的体检表呈现在系统终端,问题点会通过报警的方式同步显示出来。
徐工集合十年的吊臂检测经验,自主研制开发的智能化吊臂试验台,可以模拟各种实际作业工况,在线完成吊臂内部机电液、以及所有功能和性能的测试。
测控技术不仅仅覆盖了焊接中心、整机装配线、吊臂试验台、底盘检测线,在徐工大型高新起重机研制基地20条现代化生产线上,乃至正销往世界各地的设备上,都实现了物联网技术和ERP、MES、SRM、CRM、BI等现代化管理系统全面融合,实现了产品全生命周期管理。徐工重型的高管,只需通过系统,就能实时查阅到各类数据报表,和自动呈现出的各类异动分析。
在徐工智能化专有技术的支撑下,决定“世界第一吊”核心构件可靠性的关键问题已迎刃而解,等待它们的,是世界级测控技术的考验。藉此,经过多年磨砺磨合,徐工超大型全地面起重机制造航母终于全面拔锚起航,开始为中国石化、风电、能源等大型项目建功立勋。
责任编辑:Hermia
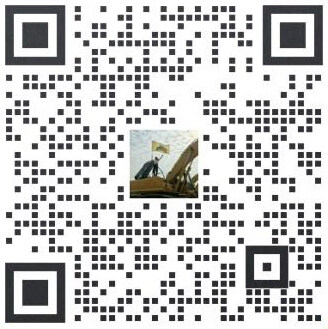
买车卖车 养车维修 疑难故障 学大招
扫码加入BOSS团徐工挖机群