难加工材料的加工技术的有效解决途径
工程机械的一些零件由难加工材料制成。充分认识难加工材料的种类、切削加工的特点及其应当使用的刀具材料,研制先进的刀具及其材料,采用新的加工技术,是解决难加工材料加工问题的有效途径。
一、难加工材料的种类
用于工程机械零件的难加工材料主要有高强度钢、超高强度合金结构钢、高锰钢、淬硬钢、冷硬铸铁、不锈钢、高温合金、工程塑料、复合材料等。其难加工的原因一般是高硬度、高强度、高塑性和高韧性、低塑性和高脆性、低导热性、有微观的硬质点或硬夹杂物以及化学性质活泼。为此,应针对难加工材料的特点,采用新的加工技术,保证加工效率和加工质量。
二、难加工材料切削加工特点
1.高强度和超高强度钢
高强度、超高强度钢与普通碳素结构钢相比,硬度和强度比45钢高出1倍以上,冲击值较大,导热系数偏低,故切削力较大,切削温度较高。
加工高强度、超高强度钢时,应根据粗加工、半精加工、精加工的要求,分别采用不同牌号的YT类硬质合金刀具。高速精加工时,应采用高碳化钛基(TiC)含量的YT类合金,也可采用YN类合金(金属陶瓷)、涂层合金与Al2O3陶瓷。在工艺系统钢性允许的情况下,应使刀具的前角和主偏角较小,刀尖圆弧半径较大。加工时,则必须采用低于加工中碳正火钢的切削用量和切削速度。
2.高锰钢
常见高锰钢的典型牌号有Mn13、40Mn18Cr3和50Mn18Cr4等。其原始硬度虽不甚高,但其塑性和韧性特别高,加工后硬化可达HBW500,导热系数只为45钢的1/4,切削力比加工中碳钢时增大60%,切削温度很高。
切削高锰钢时应选用硬度高、有一定韧性、导热系数较大、高温性能好的刀具材料。粗加工时一般应选用YG类和YW类硬质合金,精加工时可用YW或YT14类合金,如用Al2O3陶瓷刀具进行高速精加工,效果则很好。加工时,宜采用较小的前角、主偏角和较大的后角;切削速度应较低,进给量应较大。
3.淬硬钢和冷硬铸铁
淬硬钢的硬度可达HRC60以上,塑性和导热系数均极低;冷硬铸铁的硬度可达HRC52~HRC60,其他性能与淬硬钢相近。这2种材料宜采用YG类合金(YG类的弹性模量大于YT类合金)。若用Al2O3或Si3N4基陶瓷刀具对淬硬钢和冷硬铸铁进行精加工、半精加工,效果比硬质合金更好。加工时,刀具应采用较小的前角、主偏角和较低的切削速度。半精加工和精加工时可用CBN立方氮化硼刀具。
4.不锈钢和高温合金
奥氏体不锈钢(如1Cr18Ni9Ti)加工难度较大,它的原始硬度、强度都不太高,但塑性、韧性很高。加工时硬化严重,且有一定数量的硬质夹杂物,导热系数仅为45钢的1/3,切削力较大,切削温度较高。
高温合金的加工难度更大,其原始硬度、强度偏高,导热系数很小(为45钢的1/3~1/4),硬夹杂物多,加工硬化严重,切削力大,切削温度高。加工不锈钢和高温合金都应采用YG类和YW类硬质合金,而不能用含Ti的YT类合金。加工时应采用适当的刀具前角,切削速度应较低,进给量应较大。
5.工程塑料
工程塑料的品种非常多,按其性质的不同可分为热塑性塑料和热固性塑料2大类。其硬度、强度虽然不高,但导热系数极小,只为碳钢的1/175~1/450,加工时容易引起烧伤和热变形;弹性模量小,不易保证加工尺寸。加工工程塑料刀具材料一般选用YG类硬质合金或高速钢。
6.复合材料
复合材料可以由金属、高聚物和陶瓷三者中任意两个人工合成。复合材料包括纤维增强材料和颗粒增强材料,其中纤维增强材料有碳纤维(CFRP)、玻璃纤维(GFRP)和Kevlar纤维(KFRP)等。其弹性模量和导热系数都很小,已加工表面易发生回弹、撕裂,产生毛刺;纤维对刀具切削力有一定擦伤作用,刀具材料宜选用YG类硬质合金或高速钢;颗粒增强材料的基体(如铝合金)虽较软,但颗粒(如SiC)很硬,对刀具切削力有冲击和刮伤作用,故刀具受损伤很大,应采用CBN或金刚石刀具。
三.难加工材料加工新技术
1.采用高性能新刀具新材料
新型刀具(见图1)的应用有力地提高了难加工材料加工效率。新型高速切削钢有各种超硬高速钢、粉末高速钢和涂层高速钢,其切削性能比普通高速钢大为提高。新型硬质合金包括各种添加钽、铌等元素的WC基合金、细晶粒和超细晶粒的WC基合金、TiC基和Ti(C,N)基合金、涂层和稀土硬质合金,还有热压复合陶瓷和超硬刀具材料CBN、金刚石等,可以分别用于切削各种难加工材料,但应注意工件、刀具材料的合理匹配。
2.采用非常规切削方法
上述新型刀具材料在常规切削状态下的性能尚不能满足一些难加工材料的切削需要。例如,对于某些高硬度材料的加工,新型硬质合金的硬度和耐磨性还显不足,因此必须降低切削速度,由此造成加工效率不高。CBN和金刚石刀具硬度虽高,但强度不足,且金刚石不能加工黑色金属,故只能在一定的切削条件下用于难加工材料的加工。对于以上状况,可采用非常规的新切削方法。
(1) 加热切削法
加热切削法一种是导电加热切削,即在工件和刀具的回路中(工件必须是导电体)施加低电压(约5 V)、大电流(约500 A),使切削区产生热量,从而使局部工件材料的力学性能、接触和摩擦条件都发生变化。
另一种是等离子体加热切削,即用等离子弧对靠近刀尖的工件材料进行加热,使其硬度、强度降低,从而改善了切削条件。
这2种方法的效果相近,均可较大幅度地降低切削力,消除积屑瘤,提高表面粗糙度技术标准和刀具耐用度。因此用这样的方法进行大切深、大进给加工硬材料是有效的。沈阳工业大学和北京理工大学曾用等离子体加热切削法加工高锰钢和高强度钢,华南理工大学和安徽工学院曾用电热切削加工高强度钢,取得了系统的试验数据,并开始在生产中应用。此外,还有一种激光辅助切削法,如图2所示。
近年,国内发明了“电熔爆”切削法。带电的刀盘与被加工表面产生剧烈放电,将被加工表层快速熔化、爆离,从而切掉余量。此方法工件内部材料不受热的影响,效率高,对硬、软、黏料均适用,既可用于粗加工,又可用于精加工。
(2) 低温切削法
低温切削法用液氮(-180 ℃)或液体CO2(-76 ℃)为切削液,可降低切削区温度,如图3所示。据试验,使用该方法主切削力可降低20%,切削温度可降低300 ℃以上,同时积屑瘤消失,提高了已加工表面质量,刀具耐用度可提高2~3倍,在加工高强度钢、耐磨铸铁、不锈钢、钛合金时均有效果。
(3) 振动切削法
振动切削法是用不同形式的振动发生器,使刀具发生强迫振动。f >10 kHz者为高频,f<200 Hz者为低频。振动切削可使刀屑间摩擦系数和切削力大幅度降低,变形系数及切削温度下降,积屑瘤消失,加工硬化降低,故能提高已加工表面质量。但对刀具耐用度有些不利,必须采用韧性强的刀具材料(如高速钢、超细硬质合金等)。国内有10余所高等院校及研究所对振动切削进行过研究,被加工材料涉及钛合金、淬硬钢、不锈钢、热喷涂层、紫钢、陶瓷及GFRP等,加工方法有车削、攻丝、钻孔、铰孔等,都取得了好的效果。若同时使用切削液,效果尤佳,如图4所示。
(4) 真空切削法
日本东洋大学对真空中切削进行了研究,加工铜、铝时,真空度对变形系数、切削力及已加工表面粗糙度无影响;而加工中碳钢和钛合金时,真空度越大,其变形系数及切削力加大,表面粗糙度较低。这是因为在真空中刀屑界面不能产生有利于减小摩擦的氧化物。图5为真空切削的零件。
(5) 惰性气体保护切削法
这是针对切削钛合金这类材料所采取的一种措施。南京航空学院曾在钛合金的切削区喷射氩气,使切削区材料与空气隔离,因而不产生不利于加工的化合物,从而改善了钛合金的加工性。这种方法对化学性质活泼金属的加工有一定效果。以此类推,如果采用某些特殊成分的切削液,也会有效果。
(6) 绝缘切削法
在切削过程中,如将工件、刀具连成回路,回路中有热电流,则刀具磨损加剧;如将工件、刀具与机床绝缘,切断电流,则刀具耐用度有所提高。西北工业大学用这种方法钻削高温合金K14,西安黄河机械厂用该法切削1Cr13、2Cr13钢,均取得了一定效果。这种方法的机理虽未查明,但简单易行,有实用价值。
(7) 超高速切削法
在常规切削下,提高切削速度将使刀具耐用度降低。有人提出,当切削速度提高到一个临界值,切削温度就达到最高值,然后温度将随着速度继续提高而降低,切削力也随之下降,可获得较高的表面质量。这就是超高速切削的理论基础。美国、德国、日本的学校和工厂在这方面有很多实践,他们用硬质合金、陶瓷刀具切削钢、铸铁、钛、铝合金等材料。这种切削方法常受到设备条件限制而不能推广,能否在难加工材料切削中发挥作用,尚有待探讨。
3.采用特种加工方法
工程机械零件的加工,除了上述各种方法以外,相继研究出一些与切削加工原理完全不同的加工方法,如电火花加工、电解加工、超声加工、激光加工、电子束加工、离子束加工等被称为特种加工方法。
在特种加工方法中,工具与工件基本上不接触,加工时无明显的机械作用力,可加工脆性材料、精密细微零件、薄壁和弱刚性零件等。该方法利用电能、化学能、声能、热能去除被加工材料,瞬时能量密度很高,可加工任何高硬度材料。
目前,电火花加工多用于加工模具和异形孔等;电解加工多用于加工特形表面和异形孔,可获得更高的表面质量;超声加工可加工许多非金属硬脆材料,尤其是加工异孔、切割等;激光加工主要用于各种金属、非金属材料的打孔与切割;电子束加工主要用于打微孔和切缝;离子束加工可对零件表面进行超精密、超微量加工。
这些特种加工方法都需要特殊的专用设备,价格较昂贵,消耗能量很大,因此使用范围受到很大限制,然而已在难加工材料的加工中发挥了很大作用,而且有着广阔的发展前景。
责任编辑:Ben
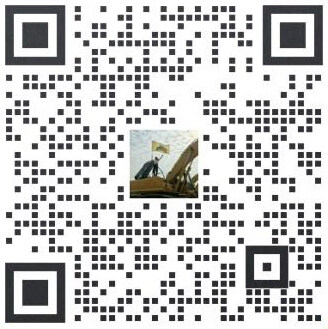
买车卖车 养车维修 疑难故障 学大招
扫码加群 BOSS团同行好友等你交流