“5G+工业互联网”来了,工厂将有哪些变化
在高速率、大带宽、低时延的5G时代,不仅将带来手机网速的成倍翻升,还将赋能各大产业,推动工业互联网发展,助力制造业提质增效和实体经济转型升级。
基于5G,机器的电缆“尾巴”将成为历史,远程操控机器人成为可能,厂区的AGV机器人实现自动巡航,仓库实现无人化管理。目前,基于5G的柔性生产已经走进现实,5G带来的不仅是网络的改进,还有生产工艺的提升,更带来了整个工厂架构的重构。
小车自动跑仓库
通过5G网络集中控制和调度,智能小车能沿着规定的导引路径行驶、清点零部件和驾驶操纵。这是中国电信浙江公司联合正泰集团打造的全省首个5G﹢MEC边缘计算智能车间里的场景。小车基于电信5G网络高带宽、低时延的特性,配备了AGV(自动导引设备)控制端软件,实现仓库无人化运作。
走进浙江正泰低压电器数字化车间,一眼望去,已看不到工人伏案工作的流水线,取而代之的是忙碌灵活的机械手臂、焊光闪烁的焊接机器人、上下翻转的自动包装机台……它们以工业互联网云平台为“大脑”,以信息化系统为“神经”,以自动引导无人AGV物流系统为“血液”,实现各功能区域高效融合,和着有序的生产节拍,共同奏出流畅的智能制造协奏曲。
在正泰集团正全力建设、即将施工完成的物联网传感器产业园区,正泰(乐清)科技创新创业园有限公司副总经理黄冰融介绍,5G赋能让企业的转型发展有了更多的可能。
“实现无线化的柔性生产,好比以前生产线是从1到10,更新换代就要换一条新的生产线,现在我们可以重新打乱组合,灵活可靠部署,有效降低了网络部署和维护成本。”
车身焊接有了“5G监工”
在几十米远的厂区,几十个机器人正挥动着手臂,对着车框上下翻飞地焊接着,不时飞溅出红色火花。“原来这些焊机都需要用网线跟服务器连接起来,都有一条长尾巴。但部署成本高、工期长,调试受地点限制,采用5G通信后,使得群控系统部署灵活,现场调试不再受地点限制,还节省了人力,提高了工作效率。”张苏强介绍,用了电信5G网络后,一台服务器可以控制整个车间的焊接设备,可以对焊接过程参数实时记录,可追溯和提升焊接质量。
而对于汽车厂商来说,车辆软件刷写是一大难题。因为一辆车一般有30~40个车载控制单元,模块软件大小不一,单台车刷写需要1个多小时,严重影响车辆下线速度。现有的车辆刷写方式,一般采用VCATS设备—网线—OBD—车辆的方式,刷写距离受到网线长度的制约,无法远程刷写。运用5G无线技术后,可实现5G网络覆盖区域的无人值守刷写,也可以实现运输在途刷写,大大扩大了刷写区域的范围。“以前软件刷写要1个小时,现在只要几分钟,5G确实是提高效率的一大利器。”吉利工程师谢志鹏表示。
在吉利汽车研究院二楼的远程控制中心,工程师可以远程实时看到工厂机器人的工作情况,还可以实时查看各种数据。“以前机器人出现故障,我们都要到现场去看,现在只要翻看数据,利用VR技术对故障进行远程诊疗,给出初步结论。”工程师王建伟表示,利用5G网络传输速率快的特点,可以实现远程工厂三维场景实时跟踪重现,相关人员可以更直观地了解工厂状态。
据悉,在吉利汽车研究院(宁波)有限公司验证中心,目前成功测试的5G应用场景有车辆软件刷写、PTL物流系统实时连接、物流仓库堆垛机信息交互、AGV系统信息交互、BOSCH群控系统、工厂的远程管理等。
浙江的“5G+工业互联网”
工信部3月24日提出,实施“5G+工业互联网”512工程,打造一批“5G+工业互联网”内网建设改造标杆网络、样板工程。浙江的动作比较快,除了浙江电信、正泰和吉利的“5G+工业互联网”实践,浙江移动等企业也已率先布局。
继在杭州建成全国最大规模的5G试验网之后,浙江移动利用5G先行先发优势,发挥5G产业联盟聚力作用,密集推进5G、人工智能、物联网、云计算、大数据、边缘计算与各大产业应用的融合创新,目前已形成应用示范点21个。
3月底,浙江移动宣布在5G工业互联网方面取得重大突破——通过与杭汽轮集团、浙江中控、新安化工等企业的合作,研究实现包括5G三维扫描建模检测系统、仪表无线减辎升级等省内首批5G工业互联网应用,且均已进入试点阶段。
“2018年10月以来,我们与杭州汽轮集团一直在5G技术结合工业互联网探索创新这一课题上不断沟通,成立了5G智能制造创新实验室,通过5G网络覆盖、终端产品与杭汽轮应用场景及需求的对接,结合第三方软件开发商和机械设备制造商的资源和能力,加上华为等通信设备制造商的技术支持,打造和孵化5G工业互联网创新应用,推动装备制造业高质量发展。”浙江移动工作人员介绍。
在杭州汽轮集团的操作车间,工作人员正用一台精密的电子扫描设备对着一台汽缸设备进行立体扫描,车间的另一边,一台电脑设备的屏幕上同时显现了实体扫描的三维模型。通过与标准模型的比对,电脑可以实时判断该产品误差率是否在正常范围内,如果产品合格,图形显示为绿色,如果不合格,图形则自动显示为红色。
杭州汽轮集团的工作人员介绍说,叶片和汽缸是工业汽轮机的核心零部件之一,杭汽轮根据客户需求“量体裁衣”式制造的零部件外形结构复杂,精度要求极高。以前传统的检测程序需要人工与设备结合进行,一个叶片的检测时间需要2~3天,外协单位的制作产品还需要专程送检,因此质检只能采用抽检的方式进行。“目前与浙江移动合作打造的5G三维扫描建模检测系统,通过激光扫描技术,可以精确快速获取物体表面三维数据并生成三维模型,通过5G网络实时将测量到的海量数据传输到云端,由云端服务器快速处理比对,确定实体三维模型是否和原始理论模型保持一致,同时向工厂实时反馈结果。该系统使得检测时间从2~3天降低到3~5分钟,在实现产品全量检测的基础上还建立了质量信息数据库,以便于后期质量问题分析追溯,既节省了成本,也直接提升了效益。该系统已在我们集团的静子车间投入试用,主要用于扭叶片的质量检测和汽缸毛坯的检测比对。”
(来源:人民邮电报、新华网)
责任编辑:Keyi
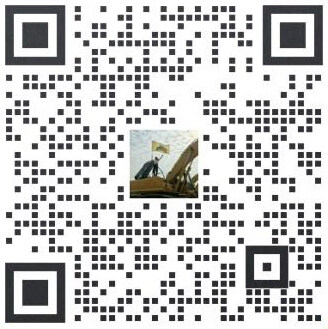
买车卖车 养车维修 疑难故障 学大招
扫码加群 BOSS团同行好友等你交流