联手华为、中国电信 海螺集团深度融智驱动产业升级
近年来,移动互联、大数据、云计算等新一代信息技术发展迅猛,智能终端、高端芯片、5G技术研究与应用催生众多产业变革和技术创新。在“十三五”开局之年,海螺集团召开了科技创新工作会议,按照新发展理念,明确了“工厂智能化、管理信息化、产业绿色化”的发展思路。随后,以“两化融合”为主线,历时两年,于2018年在全椒海螺建成投运了国内首个水泥生产全流程智能制造示范线。
智能是深入的人机交互
自动化不是智能化,信息化也不等同于智能化,真正的“智能”是人机交互,突出人在智能系统中的核心地位,机器智能和人的智慧真正地集成在一起,互相配合,相得益彰,在人的管理思想指导下,智能系统可独立或协助承担分析、判断、决策等任务,海螺打造的就是这样的智能工厂。
“专业水平最高、实践经验最丰富、操作能力最强的一批海螺人,他们最实用的生产管理思想、最高的标准要求通过智能系统得到贯彻执行”,海螺集团技术中心副主任詹家干介绍说,全椒海螺智能工厂项目集成了海螺30多年来在生产、技术、管理等方面的运行经验,通过与系统的交互融合和协调优化,最终固化下来,最大限度地保证设备安全稳定运行,提高设备运行周期和产品质量,提升管理效率和劳动生产率。
全椒海螺智能工厂包含数字化矿山管理系统、专家优化控制系统、智能质量控制系统、设备管理及辅助巡检系统、能源管理系统、供销物流管理系统和生产制造执行系统七大系统,各子系统有序推动和贯通运行,实现了工厂运行自动化、故障预控化、管理可视化、全要素协同化、决策智慧化,进一步提升了工厂运行质量、经济效益和安全环保水平。
采矿是最高效的数字运算
“从爆破、开采、铲运调度、破碎到化验检测和配矿,依靠人为组织安排,矿山开采管理很难实现并保持最优,现在矿山开采实现了高效的数字运算。”全椒海螺矿山分厂副厂长支龙告诉记者,矿山开采管理是一项极为复杂的工程,矿山数字化管理系统运行后,一切都变得简单了,有效解决了矿山生产方面存在的配矿、监督和管理问题。
在全椒海螺数字化智能化矿山管理中心,基于三维数字化建模,电子屏上清晰再现整个矿山的实时开采状态;通过跨带分析仪在线监测分析,不同点位矿石氧化钙、镁、硅、硫、碱含量也即时显示,指导配矿;人工调度已经转为自动智能调度,矿车在矿山上有序穿行。
分管采矿工作的矿山分厂厂长助理牛彪表示:“以往人工取石、化验、配矿配料,在精细化的配矿系统面前显得极为粗糙和低效,如今各处矿石品位通过系统即时被计算出来,配矿更科学,质量更稳定,资源利用率更高。”
“系统根据分析运算结果进行智能调度,不会因为人为调度导致有些矿点无车可装,有些矿点扎堆排队装车,铲运效率显著提高。”铲装驾驶员张伟说,他们现在结余了更多时间开展绿色矿山创建、专业技术培训和车辆检修保养。
2019年上半年,全椒海螺下山石灰石堆平均氧化钙合格率100%;破碎机台时产量同比显著上升;吨石灰石柴油、轮胎消耗同比均下降;出矿难的高硅、高镁低品位物料得到有效搭配利用。
质控是真正的深度“智”控
“智慧”是质控处全体员工对智能质量控制系统的一致印象。“炮弹”输送系统快速完成物料样品的自动取样和输送,跨带中子活化分析技术实现了对下山石灰石、进厂原煤实时在线检测,智能中央化验室能够对样品进行自动制样和自动检测,设定熟料产品目标值后,系统将根据原燃材料成分品质,经过数据分析计算,即时提供配料方案,科学有效地指导配料生产。
“对我们来说最直接的好处,就是不用再反复去现场取样化验了,质控工作全面提升的同时,也极大降低了我们的劳动强度。”配料主管党松利介绍说,全椒海螺质量控制系统实现了从取样、输送、制样、检测、分析、配料全流程的自动、智能控制,提升了熟料、水泥生产过程及出厂产品质量的稳定控制。
“水泥和熟料样品都分别由每天12个提高到24个,入窑生料样品由6个提高到24个。”党松利说,系统运行后,检测效率和准确度提升了,系统能够实现连续自动取样检测,避免人为干扰,取样代表性和数据可靠性得到保证,中子活化分析、荧光分析使样品成分一览无余。2019年上半年,系统检测样品31260份,为准确生产配料提供了及时、充足、准确的数据支撑。
智能质量控制系统融入海螺集团对质量控制的创新理念,运用信息交互集成和自适应控制等技术,调整操作优化工艺,产品质量管控手段得到进一步强化,质量指标稳中有升。同时,通过石灰石在线检测数据与数字化矿山管理系统的互通,实现低品位石灰石的高效开采搭配,提升了资源利用率。
巡检是最全面的“精准把脉”
在传统水泥工厂,想要设备运行更稳定,最主要还是要依靠巡检人员。巡检人员专业能力越强,越能更好地发现问题。但很多时候,是等到设备故障发生后再查找原因、进行处置,要保障生产运行稳定且保持在一个较高水平极为困难。
“在任何地方,通过手机或电脑终端都能实时观测设备运行温度、震动、压力等一系列参数,准确了解设备运行状态。”机械主管周斌告诉记者,设备管理及辅助巡检系统运行后,依托工业自动化网络系统以及加速度传感器、频谱分析等新技术应用,实现了生产线的智能点巡检。
“以前,无论夏日正午还是寒冬深夜,无论刮风还是下雨,从高偏远的矿山到最终的发运环节,我们每天都要定时对设备进行全面巡检。”如今的全椒海螺厂区,除了有计划、有组织的检修作业,一天二十四小时,巡检人员不需要在深夜和恶劣天气到高危位置进行巡检。这不仅极大减轻了巡检人员劳动强度,而且有效规避特殊时段巡检作业的安全风险。
“我在中控室发现任何参数异常,都可以第一时间调取对应参数和实时的监控视频,及时准确判断出设备的运行状况,操作调整‘对症下药’!”操作员马国栋说,对比人工巡检,这一系统预判故障能力更强、预知时间更早、隐蔽位置故障预判更精准。
上半年,系统超前发现设备隐患30余起,有效避免了重大设备事故的发生,预判故障能力明显高于人工判断。由于提前预知时间较长,为预检预修、备件准备等各项工作赢得时间。上半年,两条窑实现了8个单月运转率100%,4次连续运转周期60天以上。
操作源自最优秀的专家思想
由于受到生产线运行数据反馈滞后、各种参数相互制约等不确定因素影响,水泥窑工艺操作极其复杂,对操作员技能水平要求极高,即便是最优秀的操作员也不能保证持续最优操作,新型干法水泥生产线走信息化、工业化融合发展道路就成了不可逆转的发展方向。随着新一代信息技术发展和设备自动化程度的提高,现场测点手段不断丰富,生产过程的智能控制已经具备现实的可能。
全椒海螺有两台煤磨、两台原料磨、两条回转窑、四台水泥磨,核心控制全部在中央控制室实现,通常需要6-8名操作员同时作业,如今在中央控制室看到的只有2名操作员。
窑操作员马国林告诉记者:“专家优化控制系统上线运行后,能够通过自动导航方式来完成窑、磨的操作,保持生产以最优状态连续稳定地运行,也极大减轻了我们的劳动强度。”
制造分厂副厂长汤汉胜向记者介绍说,这一系统融合了海螺水泥(40.510,0.34,0.85%)专家优化操作思想,以最稳定的质量、最低的能耗、最大的产出为目标,通过高频率的数据采集、计算、分析实现对工艺过程的监控,并根据工艺过程变化对风、煤、料、窑转速、冷却机篦床等进行高频率小幅度的调整,减少人工操作带来的波动和干扰,使窑、磨运行工况始终稳定在最佳状态,从而达到提高运行效率的目标。
全椒海螺专家优化控制系统实现了运用“专家级操作员的思维”来代替操作员进行智能控制,使操作可以一直保持在“优秀操作员级”。
抢抓新一轮科技革命和产业变革的历史机遇,大力发展智能制造,是推动实施高质量发展的必由之路。海螺集团智能工厂建设,不仅为水泥行业转型升级探索新理念、新路径,也为传统工业高质量发展提供经验和启示,为加快制造强国建设贡献“海螺力量”。
当前,海螺集团正积极推进智能工厂各系统优化提升,并着手与华为公司、中国电信安徽公司进行5G业务合作,助推智能化工厂迭代升级,逐步在集团内完成智能工厂全覆盖。(来源:中国水泥网)
责任编辑:Harry
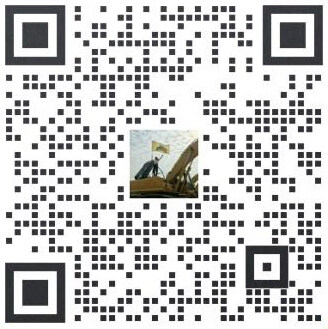
买车卖车 养车维修 疑难故障 学大招
扫码加群 BOSS团同行好友等你交流