从“刹车门”看工程机械企业如何完善质量成本管理
质量成本管理主要是控制或减少由于企业质量管理体系的不健全、产品产出过程的不合规、或者其他环节的管理缺陷而造成的质量损失,从而为企业的质量管理体系及产品质量的改进工作指明方向。
目前,中国装备制造企业普遍都处在过冬的状态下。在开源受到种种限制时,很多企业家都意识到节流是非常重要的选项。而加强质量成本管理在企业经营战略中的重要性尤为凸显。质量成本的概念是由美国质量专家菲根堡姆在20世纪50年代提出来的。其核心定义是指为了保证满意的质量而发生的支出以及没有达到满意的质量所造成的损失,而相关的所有发生的支出及损失在财务核算中都会成为企业总成本的一个组成部分。
放眼全球的装备制造领域,近年来最让人唏嘘的质量成本损失恐怕要算丰田汽车的“刹车门事件”了。
2010年初,丰田汽车公司因为“刹车门”事件,宣布在全世界召回910余万辆汽车。其核心问题出在一个非常细小的环节,驾驶座下的踏脚垫片的固定部件在设计上存在问题。踏脚垫片的纵向松动会使汽车在刹车时,踏板的一部分被前顶的垫片顶住,不能完全控制刹车,导致交通事故的发生。这个垫片固定零部件问题,导致美国有多人死亡,事故报告数达到102起,从而引起美国国家运输部和高速公路管理局对丰田公司展开司法调查。众所周知,2008年丰田汽车以897万辆的销量,力压通用汽车的840万辆,终结了通用汽车连续80多年的全球销量冠军,成为新的全球汽车霸主。丰田之所以成功,主要就是靠质量取胜,以品质赢得市场。但是值得注意的是,丰田汽车公司在快速发展过程中,为在市场竞争中赢得更多优势,不断从各方面降低成本,利润至上的理念在悄悄蚕食“品质第一”的理念。2001年底,当时的丰田CEO渡边捷昭主持制定了一个2002-2004年降低成本30%的计划,涉及80%的零部件。丰田的配套商为了仍在配套业务中获取一定利润,则必须对相应部件采取节省材料或降低产品品质的方式来降低成本,然而却使一些部件的功能性或安全性不能达到要求。为了节省成本而损失更多的质量成本是对丰田汽车“刹车门”事件的最好诠释。
“刹车门”事件不仅给丰田公司造成了超过50亿美元的直接损失,而且使丰田汽车在全世界的信誉大打折扣,多年的努力付之东流。2011年美国通用全球汽车销售达到903万辆,大众全球销售816万辆,均超越了丰田的795万辆,全球汽车行业又进入了群雄逐鹿的“战国时代”。
质量成本管理主要是控制或减少由于企业质量管理体系的不健全、产品产出过程的不合规或者其他环节的管理缺陷而造成的质量损失,从而为企业的质量管理体系及产品质量的改进工作指明了方向。概括而言,装备制造企业的质量成本管理应从以下三个方面,做精做实。
首先,企业应该建立质量成本管理的核算体系。
在一般的装备制造企业,精细化成本管理本来就是财务部门容易疏忽的环节。而明确管理质量成本更需要成本专员在每天都发生的各种成本费用中,增加其科目归集时的质量管理属性,即标示出是否是质量成本及其产生原因,并在会计核算期末将由于质量控制或质量损失发生的总成本进行统计分析。企业需要健全和完善质量成本数据的收集渠道和收集制度,建立清晰的核算程序,并系统地收集、归纳、整理质量管理体系建设、产品实现过程,预防不合格品的产生所支付的费用以及由于各种失误所产生的质量补救措施费用。当这些数据用来和标杆企业、目标成本或以往的各期数据进行比较时,质量成本的控制情况将一目了然。当然,为了让企业管理层很容易做出科学的决策,质量成本的统计分析应从不同层面反映质量成本产生的单位、部门、项目和原因,给出改进的建议,为质量方面的持续改进提供依据。
其次,质量成本管理的提升根源还来自于企业的质量管理进步。
所以装备制造企业必须做好质量管理体系建设。质量管理体系的建设核心是在研产供的各环节做好质量管理控制。优质的设计可以创造出高质量的产品,设计不合理导致生产失败所付出的成本损失是非常巨大的。也就是说,在设计阶段用于改正错误的成本,远远小于产品下线及销售出去再召回的成本损失。所以,企业在设计产品时,不仅要考虑各零部件的功能、强度,更要整体考虑产品在出售后的使用寿命或使用韧性。另外,企业一定要强化研发与工艺指导生产的工作职能,帮助企业质量部门设置合理的质量控制点,在公司内部明确一套质量标准,同时将标准有效传递给生产单位。而在生产过程中,企业则要强调现场目视化管理,使生产各环节一目了然。目视化管理包括了作业标准目视化、检验标准目视化、关键质量控制点的目视化。借助各种表格、图形、数据、颜色等明示的现场管理具有视觉化、公开化、透明化的特点,可以迅速传递生产信息、直观暴露问题、有效提高生产质量的管理水平。另外,为保证原辅材料及配套产品的质量,企业需要加强对供应商的管理。供应商的管理主要包括5个方面:供应商开发及准入评估管理、供应商产品规格及样品确认管理、供应商绩效考评管理、供应商的日常辅导管理、供应商的退出管理。其中供应商的开发准入、供应商的绩效考评最为重要。企业只有对供应商做好支持工作并实现优胜劣汰,才能有效提升自身产品的质量竞争力。
最后,质量管理的提升离不开科学的绩效管理。
企业的质量绩效管理是从技术上、管理上找出质量问题发生的原因,采取纠正及奖惩措施,避免问题重复发生。在笔者熟悉的装备制造企业中,还有不少质量管理部仍是整体质量管理及监督检查的执法部门,并不是质量责任的承担部门,这样的职责分工的结果就是很难让质量问题最终归零。企业应当明确,对产品已出货的,经公司确认的产品质量事故或批量产品未达到合格率的,质量部门应至少承担30%的处罚责任,而直接的肇事部门最多承担70%的处罚责任。这样的目的就是让质量管理部门背负质量责任并将相应的责任逐层通过价值链进行分解。质量部门在实施企业内部的质量绩效考核的关键点就是明确质量问题的范围及理清每种质量问题的原因及责任归属。这就需要企业在各环节的工作过程中形成完整而系统的管理记录,如表单、报表、问题处理报告等,这将有效地承载质量绩效考核运行。另外,优质的产品是生产出来的而不是检验出来的。在设计、生产、包装等过程中及时发现问题,从而避免造成不良后果是质量控制的最优管理手段。
很多成功的企业会实行对不良品质检奖励措施。也就是在日常工序中,检验人员或下游环节对已经发生的质量问题及时发现纠偏,问题责任人承担处罚的同时,问题发现人员将获得一定比例的奖励。这种管理模式对提高产品质量非常有效,而且激励了全员的工作责任心。
责任编辑:Nora
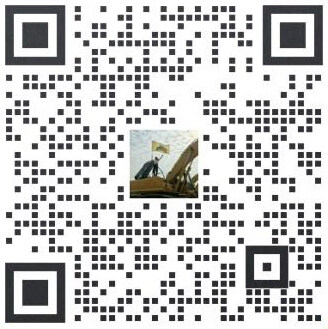
买车卖车 养车维修 疑难故障 学大招
扫码加群 BOSS团同行好友等你交流