振动压路机铰接支架的配对加工工艺
十字铰接支架是振动压路机前、后两部分的重要连接部件,其主要由支架1、球铰轴承(2、6)、十字轴3、向心关节轴承4、端盖5及转向架7(分上、下)等零件组成,如图1所示。该铰接支架均采用滑动轴承,在满足其使用要求的情况下,可大幅度降低制作成本。
1. 原加工工艺缺陷
原加工工艺如下:先将支架1和端盖5(见图2)单独加工成型,然后将十字铰接支架各个零件组装为一体。支架1和端盖5上各有1个轴承座孔,由于各部件单独加工,造成其组装后的同轴度精度不高,导致轴承受力不均,承载能力变弱,很容易使轴承受到损伤。装配时,须先用2个定位销将支架1与端盖5定位,再用10条螺栓将端盖5与支架1紧固在一起。由于支架1和端盖5单独加工,且支架1上的螺纹孔与端盖5上的连接孔在加工过程中也存在一定误差,造成支架1与端盖5紧固在一起后,支架1上的轴承座孔与端盖5上的轴承座孔的同轴度精度进一步降低。
原加工工艺缺陷主要是不能保证支架1与端盖5装配时轴承座孔的同轴度精度。为实现铰接架批量生产、同时提高加工精度,我们决定对原加工工艺进行改进。
2. 改进措施
为满足十字铰接支架装配精度要求,经研究,决定在支架1和端盖5的加工中采取配对加工新工艺,如图1所示,具体方法如下:
(1)粗加工支架和端盖
粗加工支架1和端盖5时,其轴承座孔均留有2~3m m加工余量。另外,要以端盖5上的轴承座孔为定位基准,在钻床上使用钻模钻出端盖5上的10个连接孔。连接孔直径与支架上螺纹孔的底径尺寸相同。
(2)将支架和端盖配对
加工顺序为:将支架1与端盖5之间的配合面各加工一次,以便找平。1个支架配备1个端盖,加工时将其外形对齐后,用压板工具将端盖紧固在支架上。在规定位置钻出2个定位销孔(用于支架1和端盖5定位),并装上定位销(见图3),以端盖上的10个连接孔为钻模,依次钻出支架1上10个螺纹孔的底孔。选择其中2组底孔,装入2个定位销(临时用于增加连接强度)。如图3所示。
(3)精加工支架和端盖上的轴承座孔
将完成配对的工件装在T611型镗床上,粗镗和精镗支架1和端盖5上的轴承座孔。由于这2个轴承座孔是定位后一次性镗出的,因此其同轴度非常高。
(4)完成支架和端盖的其他加工
完成配对加工轴承座孔后,将4个定位销打出,拆开这2个零件,并在其表面打上配对编号,然后分别完成单个零件的后续加工工作。后续加工工作包括端盖5上连接孔的扩孔和锪孔,支架1上螺纹孔的攻丝及其他加工工作。
(5)组装十字铰接支架
主要组装顺序如下:在支架1轴承座孔上安装球铰轴承2的外圈,在端盖5轴承座孔上安装球铰轴承6的外圈;在十字轴 3与支架1、端盖5配装的轴颈上,分别安装球铰轴承2的内圈和球铰轴承6的内圈;将支架1、十字轴 3及端盖5组装到一起,用2个定位销将支架1和端盖5进行定位,再安装10条螺栓并进行紧固;通过调节整螺栓,调整球铰轴承2、6的间隙。
3. 改进效果
按照上述加工工艺加工,该十字铰接支架轴承同轴度小于0.01m m,有效地保证了轴承的装配精度。将支架1和端盖5轴承座孔的同轴度精度提高后,装配后不产生自身应力,增强了轴承的承载能力,延长了轴承的使用寿命,整机可靠性也显著提高。经反复实验证明,该铰接支架加工工艺设计合理、简单实用、通用性强、成本较低。
责任编辑:Quasimodo
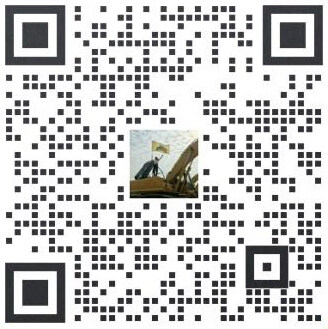
买车卖车 养车维修 疑难故障 学大招
扫码加群 BOSS团同行好友等你交流