桩基础施工新技术专题讲座(二十二)上
随着我国经济建设的高速发展,高层建筑、大型厂房、港口码头、水库坝基、公路桥梁及高速铁路等工程嵌岩灌注桩数量大幅度增加,这些灌注桩孔直径一般都较大,嵌岩深度较深,多数要求嵌入新鲜基岩面一定深度,以确保基桩的承载力和抵御自然灾害的能力。
大连海上瞄链桩
大直径嵌岩钻进技术现状
大直径嵌岩钻进技术难点分析
单位体积岩石的破碎力和单次破碎岩石所需要的临界破碎力均随岩石强度的增加而增大。因此,若要有效地破碎基岩,必须对其施加足够的破碎力(强大的钻压与扭矩及冲击力等)。碎岩断面和碎岩量随桩孔直径增大而急剧增加,从而导致嵌岩钻进破碎岩石的循环次数增多,钻进效率降低。恶劣的孔底清渣条件将导致重复破碎,结果造成钻进效率低下。
常用大直径嵌岩钻进方法分类
按碎岩方式划分 ①回转式钻进方法包括滚轮(牙轮/滚刀)钻进法、双腰带翼状钻头钻进法及钢粒环状钻进法等。②冲击式钻进方法包括纯冲击无循环钻进法和冲击反循环钻进法等。③冲击回转式钻进方法包括气动/液动潜孔锤钻进法以及可旋转式钢绳冲击钻斗钻进法等。
按成孔方式和孔形 可划分为分级扩孔法、梅花孔法、扩底法及空心桩法等。
附表为常用于硬岩基桩孔的钻进方法。
嵌岩灌注桩施工的特点及要求
钻孔浅、直径大
使用硬质合金钻头回转钻进时,现有钻孔设备对单位面积上轴压力很难达到要求,最佳的钻进方法是将静压回转切割破碎岩石改为动载冲击。
钻孔地层复杂
在一个深度十余米或数十米的钻孔内,地层变化往往很大,包括一般土层(如人工填土、淤泥、黏性土及砂类土等)和硬层(如砂砾石层及软质与硬质基岩等)。在一般土层中较容易钻进,进尺工作量大,但往往孔壁稳定性差,经常出现缩颈、塌方及超径等现象;硬层钻进量在钻孔中通常只占总进尺的10%~30%,但钻进时间要占总钻进时间的一半以上。由此可见,提高硬层的钻进效率是当前嵌岩桩钻进亟待解决的关键问题。
排粉能力强
由于钻孔直径大,孔底全面破碎,单位时间产生的岩粉量大,为保持孔底干净,免于重复破碎或埋钻,要求钻进方法应具有强有力的排粉能力。
高速度
为了使建设资金充分发挥作用,建设单位往往需要用高标价来要求缩短施工工期,而城市高层建筑往往场地狭窄钻孔密集间距小,不可能过多地增加钻机,这就要求钻进方法必须实现高速度。
气动潜孔锤反循环钻进基本原理及发展概况
基本原理
潜孔锤反循环钻进,是将潜孔锤碎岩钻进与流体介质反循环相融合,利用双壁或三通道钻具使流体介质沿中心通道构成反循环,有效保护孔壁,彻底排除孔内岩渣屑,钻进中实现反循环连续取心并有效解决孔口粉尘污染。20世纪90年代原长春地质学院殷琨教授和蒋荣庆教授在国内首先研制出大直径反循环潜孔锤钻具系统,为大直径基础工程嵌岩孔施工提供了一种高效钻进方法。
版权声明:本稿件为《工程机械与维修》杂志独家向第一工程机械网供稿,如需转载请务必标明原稿出处及作者,违者必究!
瞄链桩施工图
发展概况
气动潜孔锤有时也称气动锤、空气锤、气动潜孔冲击器等,发明应用于20世纪初,20世纪30年代中期开始发展,后经不断改进和完善,先后在一些工业发达国家得到广泛应用。20世纪40年代末,气动冲击旋转钻进出现在采矿工业中,到50年代末期已开始用于深井钻进。20世纪80年代,国外开始研究贯通式潜孔锤及全孔反循环钻进工艺方法。在欧美气动钻进中遇到硬岩层和卵砾石层时几乎95%以上都是采用气动潜孔锤钻进。理论和实践证明:在硬岩地层和软硬交错地层采用气动潜孔锤钻井技术,可大幅度提高钻井效率,防止井眼弯曲,减轻钻具和钻头磨损,减少井内事故,缩短施工周期,降低钻井成本,是目前解决硬岩钻进难题最有效的方法之一,具有广泛的应用前景。
国产气动潜孔锤的使用已有50余年的历史,自20世纪60年代以来,气动潜孔锤钻进技术发展迅速,应用领域不断拓宽,从初始的爆破孔施工,逐步发展到水文水井钻凿、地质岩心勘探、水库坝基帷幕灌浆、工程地质勘察、非开挖管线铺设、建筑基础及岩土工程等几乎所有钻孔施工领域。
国内先后研究和生产气动潜孔锤的单位有:吉林大学建设工程学院(原长春地质学院、长春科技大学),中国地质科学院勘探技术研究所,长沙矿山研究院、长沙天和钻具机械有限公司、浙江嘉兴冶金机械厂,宣化、蚌埠、沈阳、通化风动工具厂,无锡钻探工具厂,本溪、太原矿山机械厂,上海探矿机械厂,宣化英格索兰矿山工程机械有限公司等。20世纪90年代,吉林大学研制了单体大直径反循环贯通式潜孔锤和组合式大直径潜孔锤钻具系统。
近年来国内外气动潜孔锤结构及其钻进工艺上的发展趋势主要表现在以下方面:①从有阀式发展到无阀式。无阀式气动潜孔锤对气压适应性强,耗气量低。②有效长度更短、结构更简单、寿命更长。③单次冲击功由小向大发展。④钻进深度由浅向深发展,钻孔直径由小向大发展。⑤将多个单体气动潜孔锤组成集束式气动潜孔锤用于大直径钻进。⑥与多种钻孔工艺相结合。⑦应用领域更加广泛。⑧发展贯通式气动潜孔锤,集潜孔锤碎岩、冲洗介质反循环、钻进中连续取心(样)三项技术于一体的钻进技术。⑨采用计算机仿真研究潜孔锤。仿真电算揭示潜孔锤动力过程,找出配气参数、结构参数等主要因素对潜孔锤工作性能的影响规律,替代传统的实验法、经验法和类比法,实现潜孔锤参数的优化设计。
气动潜孔锤反循环钻进与气动潜孔锤正循环钻进比较
潜孔锤传统工艺方法为正循环钻进,压缩空气经钻杆内孔道传输给潜孔锤,驱动潜孔锤作功。排出的废气经钻头排气孔排出,冲洗孔底,冷却钻头,携带岩渣屑沿孔壁与钻杆之间的环状间隙上返至地表,完成正循环钻进过程。潜孔锤正循环钻进时,高速气流冲刷孔壁,不利于孔壁的稳定;气流排出孔口造成粉尘污染,不利于环保。一般情况下,当钻孔直径大于200 mm时,用于驱动潜孔锤作功的供气量小于正常排渣所需的空气量,孔内排屑成为难题,限制了潜孔锤钻进技术多领域、大面积的推广应用。
潜孔锤反循环钻进,钻杆采用双通道,压缩空气由双壁钻杆环状通道输入,经潜孔锤作功后的废气携带孔底的岩渣屑进入双壁钻杆中心通道上返至地表。潜孔锤反循环钻进有以下几方面特点:
压缩空气和上返流体介质均在封闭的双壁钻具内输运,避免了与孔壁的接触和对孔壁的冲刷,有利于孔壁的稳定,对复杂、漏失、破碎地层有独特的效果。
上返的流体介质沿双臂钻杆中心通道输运,中心通道的直径及断面积是设计时确定的,上返流速不受孔径变化的影响,从而保证足够大的上返流速(一般大于30m/s),从根本上解决了较大直径钻孔岩渣屑难以排出的工程难题。
潜孔锤正循环钻进时,由于是全断面钻进时,不会产生柱状岩芯。若采用岩芯管取芯钻进,也只能提钻取芯,与潜孔锤高速钻进不相匹配。贯通式潜孔锤配用双壁钻杆实施全孔反循环连续取芯钻进新工艺,钻进中产生的柱状岩芯在高速上返气流的托举下顺利输送至地表,实现了潜孔锤高效钻进与取芯同步进行。由于岩芯及岩渣屑被钻头克取后便直接进入钻具的中心通道内,不与孔壁接触,其岩芯样品质优良,采取率高。
潜孔锤正循环作业时,孔内排出的气流携带着渣屑由孔口喷出,粉尘弥漫,影响作业,污染环境,不利于环保。潜孔锤反循环钻进,岩渣屑及岩芯沿排渣管定向排出,易于收集与除尘,有利于环境保护。(待续)
版权声明:本稿件为《工程机械与维修》杂志独家向第一工程机械网供稿,如需转载请务必标明原稿出处及作者,违者必究!
责任编辑:Eason
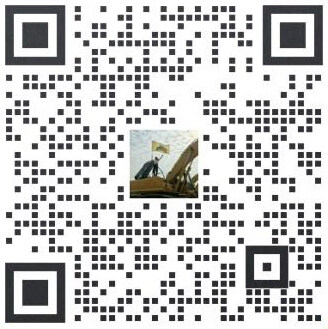
买车卖车 养车维修 疑难故障 学大招
扫码加群 BOSS团同行好友等你交流