借我一双慧眼——浅谈生产现场可视管理(下)
日本人用“改善”一词来描述永无休止的改进过程,不断制定并达到更高目标。1993年版牛津英文词典中“改善(KAIZEN)”的定义为“一种企业经营理念”,用以持续不断地改进工作方法与人员的效率。许多“独特的日本式”管理,如TQC(全面质量管理)和QCC(品管圈)等,都可以浓缩成“改善”一词来表示。因此本文将讨论能够实现现场改善的可视管理。
可视管理的“5S”
“5S”是5个日文首字母的缩写,这5个日文词为Seiki(整理)、Seiton(整顿)、Seiso(清扫)、Seiketsu(清洁)和Shitsuke(素养)。美国版本的“5S”为Sort(分类)、Stable(稳定)、Shine(光洁)、Standard(标准化)和Sustain(坚持)。尽管有名称的差异,每个S的定义实质与实施主旨却完全相同。世界各地的生产管理经验及相关研究机构未发现有任何企业不适合采用5S,不管企业的现状是“运行良好”,还是“问题缠身”,“5S”都会对其发展有所助益。可视管理也可以用“5S”的方法来构筑。
⑴整理(去除不需要的东西):现场仅能放置一些现在及近期内要使用的物品,不使用的在制品、物料、机器、工具、模具、架子、台车、箱子、文件以及私人物品统统丢掉。
⑵整顿(将需要的东西有序摆放):在现场每一项物品都必须放置在正确的地方,在需要的时候随用随取。正确标示出地面上的标线,并检查通道上是否有障碍物。这样一来,任何物品有没有定位,都很容易被发现。
⑶清扫(将机器及工作区域打扫干净):经常检查机器地面及墙壁是否干净,机器是否有异常之处(震动、漏油等)。清扫做得好,任何异常之处都会立即变得清晰可见。
⑷清洁(保持个人的干净以及每天做上述3个“S”):检查作业员是否正确地穿着工作服,是否使用安全眼镜及手套,让他们养成持续做整理、整顿及清扫的习惯,并且将之当作他们每日例行工作的一部分。
⑸素养(自律):每一个人的“5S”职责要明确规定下来。管理者要为作业员设定标准,并保证他们遵守这些标准。作业员必须将数据记录下来,写在图表上,并且依据要求做每小时、每天或每周的点检列表工作。管理者还可以要求作业员,在每天下班前将数据资料填妥,作为养成自律习惯的手段。良好的“5S”管理,意味着只要机器一运转,就能生产出良好质量的产品。
公布标准
走入现场,可视管理即能显现出现场绩效的成果。如果看到生产线旁,有多余供应物料的箱子;装载物料的台车没有放在指定的格位内;通道(供通行之用,不是一个储存场所)上放满了箱子、绳子、不合格品及地毯时,就知道发生异常了。将作业标准张贴在工作站的正前方,就是可视管理。这些作业标准,不仅是用来提醒作业员工作的正确方法,而且更重要的是,使管理人员得以判定工作是否依据标准在进行。当作业员离开了他们的工作岗位时,管理者就知道有了异常现象,因为,挂在工作站正前方的标准作业表,明确规定了在工作时间内作业员应在哪工作。作业员不能在周期时间内完成他们的工作,管理者就无法期望他能达成预期的生产目标。
虽然“标准”记述了作业员该如何做好他们的工作,却经常没有明确记录,在异常发生时该如何处置。因此标准首先应当记述如何确认异常,然后再列出应如何处置的步骤。
每日的生产目标也要可视化。每小时及每天的目标,要陈列在公告栏上,其旁边记录实际产量数值。此项信息能给督导人员预警,以采取必要的对策,以达成目标,例如调动人员支援进度落后的生产线。现场所有的墙壁,可以转变为可视管理的工具。下列的信息,应张贴在墙上及工作本上,让每一个人知道QCD的现状。
⑴质量信息:每日、每周及每月的不合格品数值和趋势图,以及改善的目标,不合格品的现物应当陈列出来,给所有的员工看,引以为戒;⑵成本信息:生产能力数值、趋势图及目标;⑶工时;⑷交期信息:每日生产图表;⑸机器故障数值、趋势图及目标;⑹设备总合效率(Overall Equipment Efficiency,简称OEE);⑺提案建议件数;⑻质量圈活动。对每一特定的流程,也许需要再公布其他的信息项目。
设定目标
可视管理的第三个目的是使改善的目标能清晰化。假设有一家工厂接到订单,要求必须在6个月内降低某一特定冲床的换模时间。在此例中,管理者可以在机器旁边,设立一块布告栏。首先,将现在的换模时间(举例来说,3月份为6小时)画在图上。其次,再画上目标值(9月份为2小时)。然后在此两点之间连接成一条直线,表示出每个月所需达成的目标值。每次换模时都测定时间,然后标在图上。为协助作业人员达成目标,还要给予他们特别的训练。
一段时间后,难以置信的事情发生了:图上的实际换模时间,开始沿着目标直线走。这是因为作业员对目标有了认识,而且了解到管理部门期望他们达成目标。无论何时,一旦换模时间的数值跳到目标线之上,他们就知道有异常(如工具遗失等)发生了,然后采取行动,以避免往后再犯这样的错误。数字本身并不足以激励员工,重要的是目标值。
松下电气的每一位工人,每天要做400个产品,每个产品要焊10个焊点,一天总共要焊4000个焊点。假设一个月工作20天,那么就要焊8万个焊点。而焊锡工人被要求缺点率必须维持在很低的水平,每50万~100万个焊点中,不得有1个以上的缺点。到松下工厂参观的访客,经常会对工人从事如此单调的工作,而又不会发生严重的失误感到惊讶。然而,仔细想想人类所做的另一种单调的工作,以走路为例:我们终生都在走路,一而再、再而三重复极度单调的相同动作,但是仍然有些人,像奥林匹克运动会的竞走、长跑和短跑选手,致力于打破记录,因为那是他们奋斗的目标。同样的道理也可以说明在工厂里应如何达成质量控制的目标。如果管理人员能够让员工有“明确的追求目标”和“执行任务的使命感”,那么,即使在单调的工作中,员工也能保持工作的兴趣和热情。
改善的终极目标,就是要实现最高管理部门制定的公司年度以及中、长期方针。要将这些方针可视化,往下一级管理阶层逐层展开,陈列在工厂的大门口、餐厅以及宣传栏等处,最终传达到生产现场,让每一个员工都知道为何必须要从事改善的活动。当现场的作业员了解到,改善活动与公司的经营策略相关,就能更大地调动他们的工作积极性。
可视管理有助于认定问题,凸显出目标与现状之间的差异。换言之,它是稳定流程(维持的功能)、改进流程(改善的功能),鼓舞现场员工达成管理目标很有效的工具。将达成的目标及向目标前进的趋势以可视化的方式表现出来,使员工发掘更多的“改善”机会,提高他们的工作绩效。(续完)
版权声明:本稿件为《今日工程机械》杂志独家向本网供稿,如需转载请务必标明原稿出处及作者,违者必究!
责任编辑:Daisy
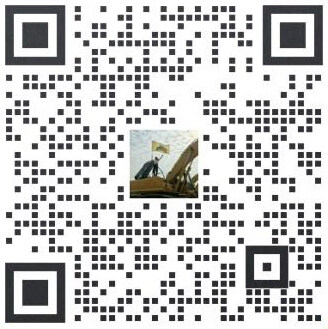
买车卖车 养车维修 疑难故障 学大招
扫码加群 BOSS团同行好友等你交流
无锡雪桃环保型沥青混合料生产线助杭州某沥青混合料生产基地投产
杭州联振是无锡雪桃老客户之一,对雪桃产品的质量比较认可,特别是其最新推出的室内环保型沥青混合料生产线[详细]2022-10-19 10:16