三一旋挖钻大全
- 三一SR285R-C10旋挖钻
- 三一SR235-S旋挖钻
- 三一SR155-C10旋挖钻
- 三一SR360R-H10旋挖钻
- 三一SR405R-HK旋挖钻
- 三一SR265-C10旋挖钻
- 三一SR415R-H10旋挖钻
- 三一SR165-C10旋挖钻
- 三一SR65-C10旋挖钻
- 三一SR205-C10旋挖钻
- 三一SR235-C10旋挖钻
- 三一SR305R-S旋挖钻
- 三一SR235-W10旋挖钻
- 三一SR485R-H10旋挖钻
- 三一SR125-C10旋挖钻
- 三一SR285R-M旋挖钻
- 三一SR445R-H10旋挖钻
- 三一SR185-C10旋挖钻
- 三一SR580R-H11旋挖钻
- 三一SR205-S旋挖钻
- 三一SR215-C10旋挖钻
- 三一SR235-M旋挖钻
加快数字化智能化转型,三一打造“灯塔工厂”样本!
近日,证券时报对三一重工桩机工厂获评全球重工行业首家“灯塔工厂”进行专项报道,报道内容如下:
三一重工(600031)北京桩机工厂日前入选世界经济论坛(WEF)新一期全球制造业领域“灯塔工厂”名单,成为了全球重工行业首家获认证的“灯塔工厂”。
实际上,北京桩机工厂只是三一重工推进数字化、智能化转型的一个缩影。那么,该工厂如何实现降本增效?公司“灯塔工厂”建设还有些规划?对于行业而言,制造业数字化转型还面临哪些难题?带着这些问题,9月29日,证券时报·e公司记者实地探访了三一重工北京桩机工厂,并对公司相关负责人进行了采访。
同等厂房面积产值翻番
三一重工北京桩机工厂位于北京市昌平区南口产业园,占地面积40000平方米,是全球最大的桩工机械制造基地,也是全球重工行业智能化程度最高、人均产值最高、单位能耗最低的工厂之一。
加快数字化智能化转型,三一打造“灯塔工厂”样本!
首先,走近工厂装配柔性岛,进入眼帘是数台机器人忙碌有序的工作。附近只看得见一两名工程师,在机器连成的生产线间偶尔走动。
“以前这条生产线上满满都是人。”三一智能制造研究院院长董明楷介绍,在这里组装的桩机动力头重达数吨,是桩机的核心部件。依托5G高清传感器,重载机器人准确地将大件送入机台,几分钟内就实现了精准组对,误差仅0.3mm,而在过去,这道工序只能靠人工“吊龙门”完成,不仅劳动强度大,效率也比较低。“这样超大部件的无人化装配,在行业尚无先例”。值得指出的是,这里的机器人拥有机器视觉也是北京桩机工厂最大特点之一。董明楷介绍,5G高清传感器就是机器的“慧眼”,每秒可产生100万个三维数据坐标,拥有强大的感知和运算能力,“有了它,无论什么型号的大大小小零件,机器人都能实时得到场景深度信息和三维模型,作业时自动修复偏差”。
据了解,目前,这一条柔性装配线可以满足3吨到16吨所有动力头的生产,自动化率70%,产能翻倍,因磕碰导致的质量缺陷已全部杜绝。
在焊接工作岛内也是同样的场景。机器人通过激光“观察”坡口环境,自适应调整参数,一次性实现厚40mm、宽60mm的高强钢多层单道焊接,解决了钻杆方头焊接这一全球行业难题。现场工人表示,机器人相当聪明,焊缝的位置存在偏差,焊接方法就会立即调整,质量不会有任何偏差。
加快数字化智能化转型,三一打造“灯塔工厂”样本!
目前,工厂里小到一块钢板的分拣,大到十多吨桅杆装配,已全部可由机器人自动化完成。桩机工厂工艺工程师侯勤华介绍,“机器视觉系统,真正赋能了机器适应环境、柔性完成任务的能力。”
三一方面提供的数据显示,经过自动化、数字化、智能化升级后,三一桩机工厂共有8个柔性工作中心,16条智能化产线,375台全联网生产设备。该工厂较改造前,工厂焊接、装配、机加等核心工序作业效率分别提升130%、100%、68%,在同样的厂房面积产值翻了一番。目前,该工厂可生产近30种机型。
三一加快数字化智能化转型
实际上,北京桩机工厂只是近年来三一重工推进数字化、智能化转型的一个缩影。
公司8月30日发布的半年报显示,公司通过深度融合制造运营系统(MOM)、物联网管理平台(IOT)、车间物流管理系统(WMS)、远程控制系统(RCS)、智能搬运机器人(AGV)等系统,构建三一智能制造管理平台,形成生产制造的“工业大脑”。
北京桩机工厂只是近年来三一重工推进数字化、智能化转型的一个缩影。
上半年,公司推动7家灯塔工厂建成达产,产能提升70%、制造周期缩短50%、自动化率提升36个百分点,累计已实现11家灯塔工厂建成达产,公司工艺整体自动化率大幅提升。
“除北京桩机工厂外,三一已在长沙、昆山、重庆等产业园先后启动46个智能制造灯塔工厂及智能产线项目,已实现近万台生产设备、十几万种物料的实时互联,各关键生产环节无人化、智能化大幅提升。”三一方面向记者透露。
北京桩机工厂只是近年来三一重工推进数字化、智能化转型的一个缩影。
三一集团董事、高级副总裁代晴华在参观结束后接受了记者采访。他透露,灯塔工厂是三一集团在数字化转型方面的一项重大举措,自2018年三一集团启动数字化转型以来,公司在2019年规划智能化制造转型路线,也就是灯塔工厂的建设。
“2020年,我们累计在智能化改造投入资金超过150亿,进行升级换代。从投资回报率估算,一般工厂在三年左右可以收回成本。而灯塔工厂的未来发展,公司也做了详细规划。首先,要把公司全球范围内的30多家工厂提升至桩机灯塔工厂。其次,公司还要启动桩机工厂的智能化改造再升级,让工厂从制造生产的智能化,全面走向以数字驱动的生产管理以及物流配送的智能化,助力我们五年目标,即3000亿销售额的早日实现。”代晴华说。
另一方面,三一智能生产模式的灯塔工厂全球布局也可以有效地对冲周期的影响。
北京桩机工厂只是近年来三一重工推进数字化、智能化转型的一个缩影。
代晴华告诉记者,工程机械行业普遍具有周期性。比如受去年疫情的影响,海外运费急剧增长。此外,近几月,国内工程机械需求下降,但海外需求大幅增加,这些因素都具有一定的影响。因此,在国际化规划上,三一海外包括美国工厂也会采取桩机灯塔工厂方式来进行改造升级,这样不依赖于大量的人工。
值得注意的是,对于行业而言,制造业数字化转型的最大难题还在于软件。“设计和仿真软件美国较多,工业控制软件德国的普遍,而国内在这些领域的软件很少,工业软件都面临国产替代的需要。不过,云原生技术给行业带来了机会,云原生在构建新一代的工业软件上具备后发优势,包括制造控制、5G云化控制以及云计算,国内在某些领域处于领先地位。但核心在于,复杂的工业软件要转化成云原生的工业软件,还需要投入大量的人力物力,以及行业各方的共同努力。”在代晴华看来。
责任编辑:Quasimodo
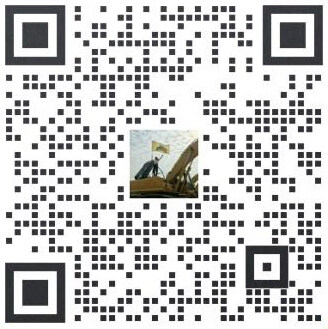
买车卖车 养车维修 疑难故障 学大招
扫码加入BOSS团三一挖机群